На каждом международном форуме по проблемам современной индустрии всегда делается акцент на таком экономическом факторе, как удлинение цепочек добавленной стоимости. То, чем занимается созданный РУСАЛом в сотрудничестве с МИСиС Институт лёгких материалов и сплавов (ИЛМиТ), как раз про это. И про алюминий в аддитивных технологиях.
О состоянии дел и перспективах использования алюминия в аддитивных технологиях рассказали в интервью нашему журналу сразу три топ-специалиста ИЛМиТ — генеральный директор Роман Вахромов, директор по науке Дмитрий Рябов и директор департамента аддитивных технологий Владимир Королёв.
Роман Вахромов,
генеральный директор Института лёгких материалов и сплавов (ИЛМиТ)
Как всё начиналось
Будучи по сути R&D-структурой РУСАЛ, ИЛМиТ имеет четыре научных направления: алюминиевые деформируемые и алюминиевые литейные сплавы, алюмооксидная продукция на основе глинозёма и аддитивные технологии. Доля «аддитивки» в общем объеме работ составляет, по словам Романа Вахромова, около 30%.
РУСАЛ выпускает около 100 различных видов продукции — пудры, газообразователи, пигменты, различные порошки. Ежегодный прирост рынка материалов и технологий для аддитивной печати на 30% не мог пройти незамеченным, и РУСАЛ принял решение развивать это направление. Развитие пошло сразу по всем направлениям — и создание в 2017 Центра аддитивных технологий в ИЛМиТ, и изготовление первых опытных партий. «РУСАЛ сделал громадное дело для распространения в России алюминия для аддитивных технологий, — утверждает Роман Вахромов. — Более чем сотне предприятий были бесплатно переданы опытные образцы порошков в обмен на обратную связь. Фидбэк помог нам понять требования наших потенциальных потребителей к морфологии и гранулометрическому составу порошков, выявлению факторов, которые могут отрицательно влиять на печать. С учётом полученной информации буквально за полтора года мы доработали технологию стандартного сплава AlSi10, и сейчас это идеальный порошок. Это правильная сферическая форма, именно тот гранулометрический состав, который обеспечивает хорошую текучесть, исключает дефекты при сплавлении».
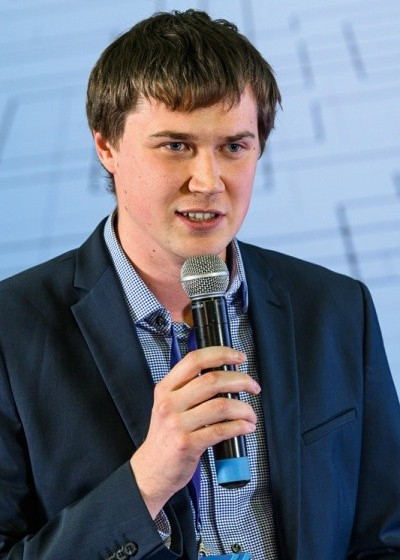
Дмитрий Рябов,
директор по науке Института лёгких материалов и сплавов (ИЛМиТ)
Положение на рынке
В 2019 году РУСАЛ продал в России чуть больше 10 тонн. Основными потребителями стали автомобилестроение, космическая и авиационная отрасли. Из крупных промышленных компаний никто, кроме РУСАЛа, алюминиевых порошков не производит. Есть, как мне объяснили, производители типа ВИАМ, которые могут произвести и поставить порошки, но производственные мощности РУСАЛ на несколько порядков больше. А вопрос о месте России на мировом рынке Дмитрий Рябов назвал едва ли не философским: «По некоторым аналитическим исследованиям, доля России по числу инсталлированных принтеров составляет 2% мирового объема, а по материалам такой аналитики вообще нет, потому что никто не знает, как посчитать. Нет единой организации, которая посчитала бы проданные порошки. Оценки рынка экспертами сильно разнятся. Но цель у нас есть — постепенно наращивать выпуск и продажу и стать производителем алюминиевых порошков номер один».
Алюминий требует технологической фантазии
Как рассказали мои собеседники, у алюминия есть козырь в виде его удельного веса, что важно для ряда изделий, где масса — решающий критерий. В принципе, конечно, любой материал найдет свое применение, но уже очевидно, что есть такие сферы, где без аддитивных технологий никак не обойтись, они, по сути, единственный способ решить какую-то задачу. Чтобы алюминий нашел достойную нишу, он должен быть лучше чем то, что сейчас используют в традиционных технологиях. Это первая задача. А вторая задача связана с мировым трендом на создание деталей под технологию, потому что чем меньше поддержек, тем процесс дешевле и быстрее. «Для этого мы сейчас нарабатываем компетенции под услуги инжиниринга, — говорит Вахромов. — Мы можем разработать материал, технологию его производства, технологию печати, делать редизайн деталей с учетом нагрузок и прочего, а также снабдить заказчика комплектом документации с информацией о том, как печатать, как производить техническую обработку и описание результатов испытанных образцов».
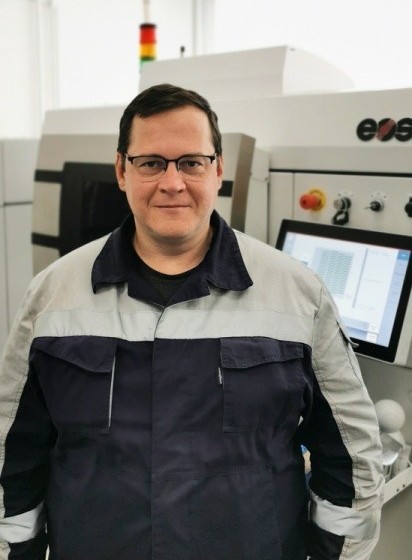
Владимир Королёв,
директор департамента аддитивных технологий Института лёгких материалов и сплавов (ИЛМиТ)
Тему продолжает Владимир Королёв: «Сейчас в каждом принтере есть режим для стандартного сплава, и многие считают, что вот купил принтер, нажал кнопку и что-то построил. Да, это может так работать, хотя там вопросы для технологов тоже возникают. А новый материал в принципе требует другого подхода. Нужна технологическая фантазия, чтобы найти оптимальный режим. В 2018 году у нас появился первый новый материал. Мы начали его пробовать и поняли, что всё происходит совсем по-другому и что режим надо создавать с самого начала».
Печать алюминием позволяет уйти от конструкторского традиционализма, погрузиться в конструкторскую фантазию. «Если до этого в течение века конструкторы были скованы существующими технологиями — можно отлить только такое, вырезать только такое, — то сейчас стало гораздо проще, — говорит Роман Вахромов. — Особенности аддитивных технологий позволяют раскрыть невероятно мощный потенциал алюминия. Как только принтеры станут подешевле, во многих секторах машиностроения станет экономически и технологически привлекательным изготовление деталей общего назначения. Мы, честно говоря, верим в теплообменники, потому что к такому большому плюсу алюминия, как его высокая теплопроводность, добавляется возможность напечатать каналы любой конфигурации».
Ограничения
«Алюминий — металл замечательный, — говорит Дмитрий Рябов. — Он не очень дорогой и хорошо обрабатывается, но аддитивные технологии пока дороги из-за высокой цены на 3D-принтеры, которая отягощает цену готового изделия. Пока в России алюминиевые порошки используются преимущественно для изготовления прототипов. Правда, например, космическая промышленность готова принимать дорогие решения, тем более что это эксклюзивные изделия, несколько штук в год. Дешевле их напечатать, чем создавать оснастку, отливать, обтачивать».
Порошки РУСАЛ печатаются на всех принтерах, что есть сегодня на рынке. В центре аддитивных технологий ИЛМиТ есть 3D-принтер EOS. Клиент, у которого такой же принтер, получит комплексное решение — материал и технологию, а для обладателей других принтеров ИЛМиТ помогает адаптировать режимы. «Основная проблема технологии, — объясняет Дмитрий Рябов, — заключается в том, что для разных принтеров под один и тот же материал нужно проводить некую оптимизацию. Проблема сертификации стоит ещё сложнее. Если в литейной отрасли мы, условно говоря, раз и навсегда сертифицируем производство проката, потом сертифицируем лист, то в аддитивном производстве надо сертифицировать конкретный порошок, да ещё в паре с конкретным принтером. А если ещё принтер одного производителя, но на нём, скажем, разные лазеры, то возникнут новые развилки требований. Ещё лет десять и придут к какой-то унификации или к понятным правилам сертификации. А пока российские и зарубежные эксперты аэрокосмической отрасли отмечают, что одна из проблем применения, по крайней мере в аэрокосмической технике, это именно проблема сертификации. Вроде правила игры всем известны, но всегда есть какие-то нюансы».
Миру нужны новые материалы
Рынок определил порошок Al10Mg как самый востребованный. Он первым был адаптирован под аддитивные технологии. «Он очень хороший, им быстро печатается, — рассказывает Дмитрий Рябов, — свойства такие же или даже лучше, чем у отливки, но проблема оптимизации массы деталей требует новых материалов. И поэтому в мире очень многие работают над новыми материалами на основе алюминия. Например, наш сплав РС 553 скандий-алюминий-магний — один из самых прочных из того, что есть, благодаря скандию. Такой сплав есть и в Европе, так называемый scalmalloy, но скандий по цене сопоставим с золотом, может, чуть дешевле. Мы в нашем сплаве снизили содержание скандия в два раза, и он стал в два раза дешевле при сопоставимых свойствах. Это практически 500 МПа, в то время как у Al10Mg прочность 300 МПа, то есть это другой уровень прочности, поэтому в каких-то применениях он может заменить титан. Порошок РС 970 спроектирован на других принципах. Это система легирования, которая классически не применяется для алюминия. Аддитивные технологии приоткрыли дверцу в некое пространство, в котором можно печатать такими материалами, которые вообще сложно получить, — они либо плохо легируются, либо плохо обрабатываются. Но мы нашли правильные компоненты, правильное соотношение, и уникальность сплава в том, что с повышением температуры он не теряет свои свойства. Для понимания: если взять обычный алюминиевый сплав и испытывать его при 100 градусах, то будем иметь около 80 процентов снижения прочности относительно той, что есть при комнатной температуре, а здесь мы имеем снижение только порядка 30%. Он очень стабильный. В этом мы видим большой потенциал, потому что жаропрочность — очень важная характеристика, и алюминий избегают применять там, где есть нагрев, а следовательно, разупрочнение».
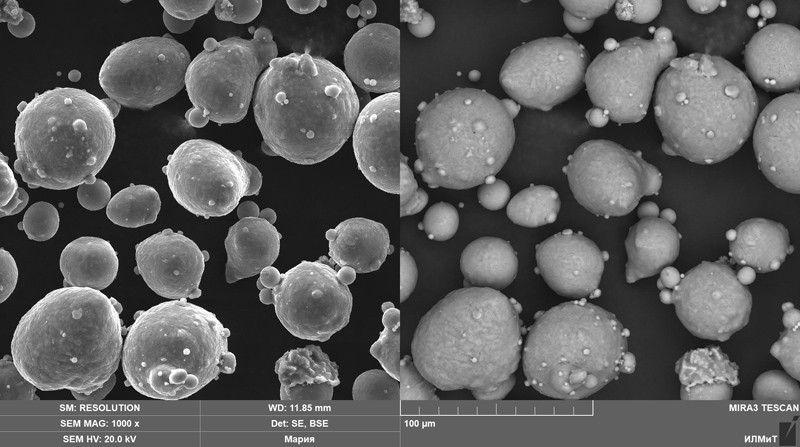
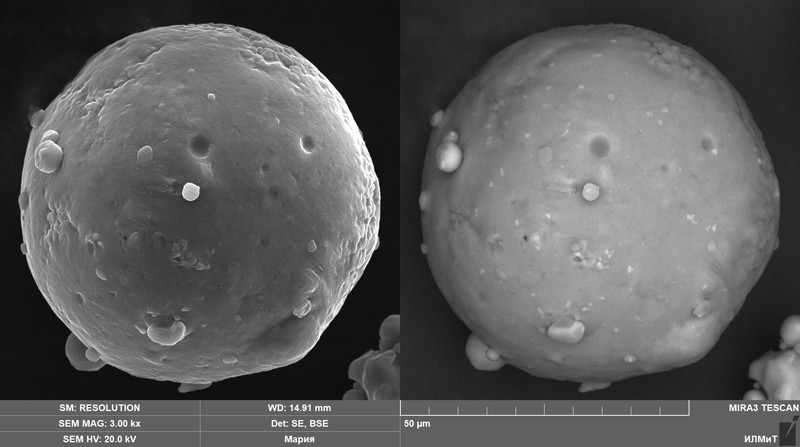
Частицы под микроскопом
Отработка экспериментальных формул
Предварительно смоделированный химический состав «овеществляют» в ИЛМиТ. Расплавляют чисто алюминиевую чушку и в строгом соответствии с технологией, в определенной очередности и с определенной температурой вводят в расплав все легирующие добавки, после чего отливают вторую заготовку. Этот слиток везут на площадку ИЛМиТ в Дмитрове, где на лабораторном атомайзере будет сделан порошок. Для экспериментов в принтере обычно достаточно 10 кг порошка, которые поступают в распоряжение Владимира Королёва. Полученный порошок имеет довольно широкий гранулометрический состав — от 1 до 250–300 микрон, и его подвергают двухстадийной обработке с целью получить нужную фракцию 10–63 микрон.
«Сначала приготавливаем кубики, смотрим, чтобы в материале не было горячих трещин, чтобы там была минимальная пористость, и также измеряем твёрдость, чтобы хотя бы примерно понимать, что в итоге получится, — излагает последовательность действий Владимир Королёв. — В итоге выбираем оптимальный режим, он должен быть самым быстрым, укладываться в требования ТЗ по сплошности материала. Только после этого порошок поступает в принтер для изготовления образцов по подготовленной сетке режимов: разная мощность лазера, разная скорость, разная стратегия движения, полосами, квадратиками, сплошная, штриховочка. Мы можем проводить более 40 видов испытаний на все виды свойств, которые интересуют реальных и потенциальных потребителей, — рассказывает Королёв. — Когда заказчик говорит, какой материал ему нужен, чаще всего он начинает с прочности, твёрдости и пластичности, а потом уже оговаривает специальные свойства — способность переносить циклические нагрузки, длительную прочность, ползучесть и другие. Далее идут такие специфичные вещи, как коррозионная стойкость, восприимчивость к различным видам излучения. Может интересовать, например, ТКЛР — температурный коэффициент линейного расширения, что очень важно, например, для космонавтов, потому что в зависимости от того, находится корабль в тени или на солнце, перепады температуры могут быть от плюс 100 до минус 60 или от минус 100 до плюс 60. Если там два материала рядом, один другого касается, у них должен быть или одинаковый ТКЛР, или должно быть полное его отсутствие. В повседневной жизни такая характеристика нам не нужна, а для некоторых потребителей это критичное требование».
Всему есть своя цена
При разработке формулы нового порошка в поле зрения присутствует вопрос цены. «Буквально 3–4 года назад килограмм алюминиевого порошка стоил около 300 евро, и его даже никто не рассматривал в качестве материала для изготовления каких-то деталей, потому что это экономически нецелесообразно, — рассказывает Роман Вахромов. — И когда была принята стратегия РУСАЛ по развитию порошкового производства, основной целью было снижение себестоимости порошка. Сейчас она составляет около 5 евро».
Разговоры о том, что аддитивная печать пока не может сравниться по точности с фрезерованием, Владимир Королёв называет палкой о двух концах: «Есть принтеры, у которых диаметр спота лазерного луча составляет 3—5—7 микрон. Для сравнения: у меня сейчас 80 микрон. Вот если у меня будет луч не 80, а 3 микрона, я буду получать точность не нынешние 50 микрон, а меньше микрона, но производительность процесса будет очень низкая. Если сейчас я печатаю, грубо говоря, 30 кубических сантиметров в час, то там я буду печатать 1 кубический миллиметр в час. Не великовата ли цена за соревнование с фрезерным станком?»
Вместо эпилога
Космическая и авиационная промышленность, а также двигателестроение — вот потребители алюминиевых порошков. Для них важны прочность и лёгкость, которые могут обеспечить только аддитивные технологии. А на недавней конференции по использованию алюминия в аддитивном производстве Роман Вахромов назвал аддитивные технологии драйвером цифровой промышленности. На мой осторожный вопрос, не является ли это утверждение поэтическим преувеличением, Вахромов уверенно ответил: «Действительно драйвер. Потому что кроме АТ нет другого производства, которое позволяет создавать продукт, что называется, с пикселя».
Сдерживающими факторами продвижения алюминиевой печати были высокая стоимость материалов и оборудования. Со стоимостью материалов, выпускаемых в промышленных количествах, РУСАЛ справился. Теперь дело за производителями 3D-принтеров. ■
Автор: Зинаида Сацкая