Как и во всех остальных рассмотренных нами технологиях, модель при FDM-печати создается послойно. Для изготовления очередного слоя термопластичный материал нагревается в печатающей головке до полужидкого состояния и выдавливается в виде нити через сопло с отверстием малого диаметра, оседая на поверхности рабочего стола (для первого слоя) или на предыдущем слое, соединяясь с ним. Головка перемещается в горизонтальной плоскости и постепенно «рисует» нужный слой — контуры и заполнение между ними, после чего происходит вертикальное перемещение (чаще всего опусканием стола, но есть модели, в которых приподнимается головка) на толщину слоя и процесс повторяется до тех пор, пока модель не будет построена полностью.
В качестве расходного материала чаще всего используются различные пластики, хотя есть и модели, позволяющие работать с другими материалами — оловом, сплавами металлов с невысокой температурой плавления и даже шоколадом.
Минусы, присущие данной методике, очевидны:
- невысокая скорость работы (но, собственно, очень уж высокой скоростью не могут похвастать и другие технологии: для построения крупных и сложных моделей требуются многие часы и даже десятки часов);
- небольшая разрешающая способность как по горизонтали, так и по вертикали, что приводит к более или менее заметной слоистости поверхности изготовленной модели;
- проблемы с фиксацией модели на рабочем столе (первый слой должен прилипнуть к поверхности платформы, но так, чтобы готовую модель можно было снять); их пытаются решить разными способами — подогревом рабочего стола, нанесением на него различных покрытий, однако совсем и всегда избежать не получается;
- для нависающих элементов требуется создание поддерживающих структур, которые впоследствии приходится удалять, но даже с учетом этого некоторые модели попросту невозможно сделать на FDM-принтере за один цикл, и приходится разбивать их на детали с последующим соединением склейкой или другим способом.
Таким образом, для очень многих образцов, изготовленных по технологии FDM, потребуется более или менее сложная финишная обработка, которую сложно или невозможно механизировать, поэтому в основном она производится вручную.
Есть и менее очевидные недостатки, например, зависимость прочности от направления, в котором прикладывается усилие. Так, можно сделать образец достаточно прочным на сжатие в направлении, перпендикулярном расположению слоев, но вот на скручивание он будет гораздо менее прочным: возможен разрыв по границе слоев.
Другой момент в той или иной мере присущ любой технологии, связанной с нагревом: это термоусадка, которая приводит к изменению размеров образца после остывания. Конечно, тут много зависит от свойств используемого материала, но порой нельзя примириться даже с изменениями в несколько десятых долей процента.
Далее: технология может показаться безотходной только на первый взгляд. И речь не только о поддерживающих структурах в сложных моделях, немало пластика уходит в отходы даже у опытного оператора при подборе оптимального для конкретной модели режима печати.
Почему же при таком количестве проблем эта технология сейчас стала столь популярной?
Главная и определяющая причина — цена как на сами принтеры, так и на расходные материалы к ним. Первым важным толчком в процессе продвижения FDM-принтеров «в массы» стало истечение в 2009 году срока действия патентов, вследствие чего за пять лет цены на такие принтеры снизились более чем на порядок, а если рассмотреть крайности (самые дорогие до 2009 года и самые дешевые сегодня), то и на два порядка: цена на самые дешевые принтеры китайского производства сегодня составляет всего 300–400 долларов — правда, скорее всего покупатель в них моментально разочаруется. Более приличные принтеры начального уровня сейчас имеют цену уже ближе к $1200–1500.

Вторым немаловажным фактором стало появление проекта RepRap, или Replicating Rapid Prototyper — самовоспроизводящийся механизм быстрого прототипирования. Самовоспроизведение касается изготовления на уже сделанном принтере частей для другого подобного принтера — конечно, не всех, а лишь тех, которые можно создать в рамках данной технологии, всё прочее приходится покупать. И оно не было самоцелью проекта: главной задачей стало создание максимально дешевых моделей принтеров, доступных даже частным энтузиастам, не обремененным излишком денег, но желающим попробовать свои силы в 3D-печати. Более того, самовоспроизводящимися (в сколь-нибудь заметной части всех деталей) были и есть далеко не все прототипы, созданные в рамках RepRap.
Мы не будем заниматься подробным описанием этапов становления проекта RepRap, разбором достоинств и недостатков таких прототипов, как Darwin, Mendel, Prusa Mendel, Huxley. Тема очень обширна, чтобы ее можно было рассмотреть в рамках данного обзора, и мы приводим эти названия только как ключевые слова для поиска информации, которой в интернете очень много.
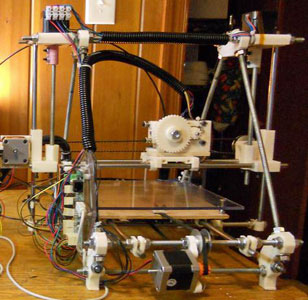
Конечно, создаваемые таким образом принтеры чаще всего далеки от совершенства даже в рамках технологии FDM, но они позволяют с минимальными финансовыми затратами создать вполне работоспособный аппарат. Нужно отметить: сегодня вовсе не обязательно искать обладателя принтера, чтобы напечатать возможные детали, и бегать по магазинам в поисках остального; предлагаются полные наборы для самостоятельной сборки принтера, так называемые DIY kits (от «Do It Yourself» — сделай это сам), которые позволяют и заметно сэкономить, и избежать лишней беготни и хлопот, да к тому же содержат подробные инструкции по сборке. Но есть простор и для тех, кто не хочет замыкаться в рамки готовых конструкций и желает внести в них что-то свое: есть масса предложений по любым отдельным комплектующим для подобных принтеров.
Еще одна положительная сторона развития проекта RepRap — появление и совершенствование различного программного обеспечения для работы с подобными 3D-принтерами, причем распространяемого свободно. В этом немаловажное отличие от аппаратов, выпускаемых именитыми производителями, которые работают только с собственным ПО.
В принципе, проект не замыкается на технологии FDM, но пока именно она является наиболее доступной, равно как наиболее доступным материалом является пластиковая нить, которая и используется в подавляющем большинстве принтеров, создаваемых на базе разработок RepRap.
Широкое распространение FDM-принтеров привело к увеличению спроса на расходные материалы к ним; предложение не могло не последовать за спросом, и произошло то же самое, что и с самими принтерами: цены рухнули. Если на старых интернет-страницах, посвященных FDM-технологиям, встречаются упоминания цен на уровне 2-3 и даже более сотен евро за килограмм пластиковой нити, то сейчас повсеместно речь идет о десятках евро, и лишь на новые материалы с необычными свойствами цена может достигать сотни долларов или евро за килограмм. Правда, если раньше продавались в основном «фирменные» материалы, то теперь зачастую предлагается нить непонятного происхождения и неопределенного качества, но это неизбежно сопутствует популярности.
Помимо цены, у FDM-принтеров есть другие достоинства, связанные с возможностями технологии. Так, очень легко оснастить принтер второй печатающей головкой, которая может подавать нить из легко удаляемого материала для создании поддержек в сложных моделях. Внеся краситель при изготовлении пластиковой нити, можно получать различные, очень яркие цвета.