Введение
TCT Asia 2025, прошедшая с 17 по 19 марта в Шанхае, подтвердила свой статус одной из ведущих мировых выставок в сфере аддитивного производства и 3D-печати, став ключевым событием в сфере аддитивных технологий Азиатско-Тихоокеанского региона. В юбилейный, десятый год своего существования, TCT Asia 2025 не только продемонстрировала впечатляющие достижения отрасли за последнее десятилетие, но и наметила векторы ее дальнейшего развития.
В этом году экспозиция объединила более 300 компаний, представивших инновационные решения в области металлической и керамической печати, фотополимерных технологий, а также автоматизированных систем для массового производства. Выставка привлекла свыше 20 000 специалистов, став важной площадкой для обмена опытом, поиска партнеров и анализа глобальных трендов.
В перечне ключевых тем TCT Asia 2025 — рост масштабов аддитивного производства, появление новых материалов и расширение применения 3D-технологий в таких стратегических отраслях, как авиакосмическая, медицинская и автомобильная промышленность. В этой статье мы рассмотрим самые значимые экспонаты и тренды выставки, чтобы понять, какие технологии будут формировать будущее индустрии в ближайшие годы.
AEE: интеграция сварки трением с перемешиванием и АТ
Компания Aerospace Engineering Equipment (Suzhou) Co., Ltd. (AEE) — один из мировых лидеров в области сварки трением с перемешиванием (FSW) — активно исследует возможности комбинирования этой технологии с аддитивным производством. Хотя основным направлением AEE остается разработка оборудования и процессов FSW, компания делает значительные шаги в интеграции этих методов для создания высокопрочных и сложных металлических конструкций.
Одно из ключевых направлений AEE — применение FSW для соединения крупногабаритных деталей, изготовленных методами аддитивного производства. Современные 3D-принтеры зачастую имеют ограничения по размерам рабочей камеры, что делает невозможным печать крупных конструкций за один цикл. Технология FSW позволяет надежно сваривать отдельные модули, сохраняя механические свойства материала. Это особенно востребовано в аэрокосмической отрасли, где критически важны прочность и долговечность соединений.
Использование FSW
Еще одна перспективная область — использование FSW для восстановления и доработки изделий, созданных с помощью 3D-печати. Метод позволяет локально ремонтировать поврежденные участки, продлевая срок службы деталей без их полной замены. В условиях растущего спроса на ремонтопригодные решения в промышленности такой подход открывает новые возможности для экономии ресурсов.
AEE обладает почти 10-летним опытом работы в автомобильной, железнодорожной, аэрокосмической, судостроительной и электронной отраслях. Компания продолжает расширять свое присутствие на международном рынке, укрепляя партнерские отношения и предлагая инновационные решения. На выставке TCT Asia AEE продемонстрировала свои компетенции и возможности, прощупывая интерес среди аддитивного сообщества. Стоит отметить, что это им удалось!
Образец монолитного днища ракеты размером диам. 3350 × 1020 мм изготовлен методом сварки трением с перемешиванием (FSW) из алюминиевого сплава 6061. Процесс производства занял 500 часов.
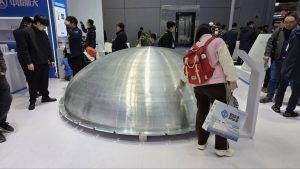
Монолитное днище топливного бака ракеты-носителя модели 3350 — один из ключевых экспонатов выставки, впечатляющий своими габаритами и передовыми технологиями аэрокосмического производства (Фото: Кирилл Казмирчук)
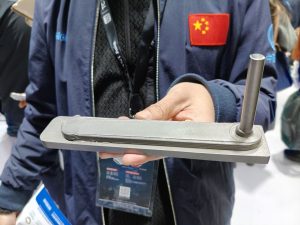
Деятельность AEE демонстрирует растущую роль гибридных подходов в современном производстве. Сочетание аддитивных технологий и сварки трением с перемешиванием позволяет создавать сложные конструкции с высокой прочностью, что особенно важно для авиакосмоса, энергетики и машиностроения. Развитие таких решений открывает новые перспективы для промышленности, делая производство более гибким и экономически эффективным.
ENIGMA: мультилазерная мультиматериальная печать
С момента основания в 2011 году компания Nanjing ENIGMA AUTOMATION CO., LTD. (далее «ENIGMA») развивается как технологический интегратор, специализирующийся на внедрении аддитивных технологий в промышленные процессы. Основной фокус внимания компании направлен на создание комплексных решений, где 3D-печать металлами по технологиям проволочной наплавки WAAM/Arc-DED (W) и LWC/LWAM/L-DED (W) становится ключевым элементом автоматизированных производственных цепочек.
Компания ENIGMA объединяет собственные разработки в области металлической 3D-печати (CML HYBRID) с передовыми австрийскими технологиями (CMT), создавая индивидуальные решения для промышленности. Специалисты интегрируют аддитивное производство с роботизированной сваркой, формируя современные производственные системы.
Однако ключевым отличием компании является технология CML HYBRID. В основе системы – многолучевая наплавка, использующая шесть лазеров с формированием кольцеобразного пятна для оптимального распределения энергии и равномерного плавления проволоки. Лазерные модели могут комбинировать различные длины волн, включая сочетание красного и синего лазеров. Такое решение значительно повышает поглощение энергии при работе с отражающими материалами, такими как медь и алюминий.
Дополнительную гибкость системе придает проволочно-порошковая подача с шестью независимыми каналами подачи порошка и проволочным питателем, позволяющая точно регулировать состав материала и создавать градиентные материалы и нанокомпозиты.
Важный элемент технологии – двухконтурная система защитного газа с независимыми внутренним и внешним газовыми контурами, которая позволяет использовать различные газовые смеси для оптимизации микроструктуры и механических свойств получаемого материала.
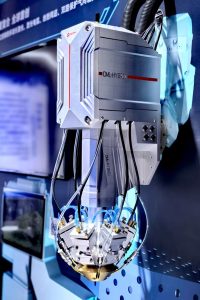
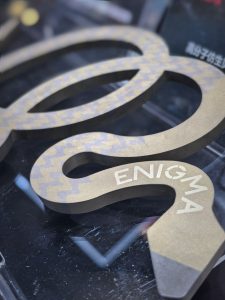
Благодаря экспертизе в металлической 3D-печати ENIGMA помогает предприятиям переходить к цифровому производству, где аддитивные технологии становятся основой для создания сложных и габаритных компонентов.
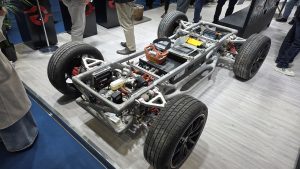
Успешный проект
Компания успешно реализовала проект по изготовлению полномасштабного шасси для электромобиля PIХ Moving методом WAAM. Образец размером 2400 × 800 × 200 мм и весом 80 кг был напечатан из алюминиевого сплава 5356, демонстрируя возможности технологии для создания массивных металлических конструкций.
Процесс печати занял 90 часов непрерывной работы (скорее всего по частям), что свидетельствует о высокой стабильности технологического процесса. От момента заказа до отгрузки готового изделия прошло всего 35 дней.
Этот проект наглядно иллюстрирует потенциал проволочной электродуговой наплавки для изготовления крупногабаритных деталей из алюминиевых сплавов, сочетая в себе высокую скорость производства с возможностью создания сложных геометрических форм. Применение сплава 5356 обеспечило изделию оптимальное сочетание прочностных характеристик и коррозионной стойкости, что особенно важно для ответственных промышленных применений.
LiM Laser – инновации в промышленной 3D-печати металлов
Tianjin LiM Laser Technology Co., Ltd. зарекомендовала себя как один из лидеров в сфере промышленных аддитивных технологий, специализируясь на разработке и производстве оборудования для лазерной 3D-печати металлов. В центре внимания компании — передовые решения на основе технологии лазерного порошкового спекания (L-PBF), позволяющие создавать высокоточные детали сложной геометрии для ответственных отраслей промышленности.
Оборудование Tianjin LiM Laser Technology поддерживает работу с широким спектром металлических порошков, включая нержавеющие и инструментальные стали, титановые и алюминиевые сплавы, а также кобальт-хромовые материалы. Все принтеры оснащены специализированным программным обеспечением, которое позволяет точно контролировать параметры печати и гарантировать стабильно высокое качество изделий.
Ключевые направления применения разработок компании охватывают наиболее технологически требовательные отрасли. В авиакосмической промышленности оборудование используют для производства сложных деталей двигателей и турбин. В медицинской сфере — для создания индивидуальных имплантатов и хирургических инструментов. Автомобилестроители ценят возможность изготовления облегченных и прочных компонентов, а в энергетике технологии находят применение при производстве деталей для газовых турбин.
Конкурентные преимущества
В числе конкурентных преимуществ решений компании – высокая производительность (до 22 см³/час при мощности лазера 500 Вт), исключительная точность построения благодаря прецизионной оптической системе, а также универсальность, позволяющая использовать оборудование как для прототипирования, так и для серийного выпуска деталей.
Центральным экспонатом стенда стала авиационная каркасная конструкция из жаропрочного титанового сплава TA15 размерами 6295 × 2198 × 614 мм, изготовленная по технологии лазерной газопорошковой наплавки (L-DED). Утверждается, что это изделие было обработано на установке со стандартными размерами камеры построения, но для реализации такого проекта пришлось сконструировать специальный подвижный стол и печатать по частям, передвигая изделие.
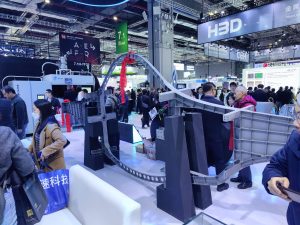
Толщина слоя структуры составила всего 60 мкм, что обеспечило высокую точность и минимальную шероховатость поверхности. При этом срок изготовления занял 62 дня — значительно меньше, чем потребовалось бы при использовании традиционных методов литья. Деталь предназначена для применения в аэрокосмической промышленности, где предъявляются особо строгие требования к прочности, массе и надежности конструкций. Титановые сплавы активно используются при производстве элементов фюзеляжей, силовых конструкций и узлов летательных аппаратов, что подтверждает востребованность данной технологии в отрасли.
Крупногабаритная печать
На выставке продемонстрировали крупногабаритный корпус авиадвигателя. Монолитная конструкция размером 1290 × 1180 × 506 мм с оптимизированной топологией, включающая сложную систему внутренних каналов и рёбер жёсткости, была изготовлена из алюминиевого сплава AlSi10Mg на промышленном 3D-принтере LiM-X1500H всего за 288 часов непрерывной печати.
Этот кейс наглядно показал, как аддитивные технологии сокращают сложные многоэтапные производственные процессы традиционного машиностроения до единой цифровой цепочки. В отличие от классических методов, требующих десятков технологических операций (литьё, механическая обработка, сварка, сборка), 3D-печать позволила создать готовое изделие высокой степени сложности за один производственный цикл с минимальными постобработками. Особое внимание специалистов привлекла реализованная в конструкции система полых структур, которая при традиционном производстве потребовала бы дорогостоящей и трудоёмкой сборки из множества отдельных компонентов.
Этот экспонат стал наглядной демонстрацией перехода от концепции к серийному производству и открывает новые перспективы для создания сложносоставных деталей в аэрокосмической отрасли, где на первый план выходят требования к весовой эффективности, прочности и точности изготовления.
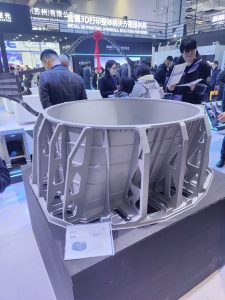
В следующих публикациях мы продолжим обзор стендов ведущих производителей, представивших свои новинки на выставке TCT Asia 2025.
TCT Asia 2025: тренды, иллюзии и китайский размах (часть 2)
TCT Asia 2025: тренды, иллюзии и китайский размах (часть 3)