Или надежное аддитивное производство сегодня и повторяемость завтра
Еще не так давно успешное создание единственной детали с помощью 3D-печати было поводом для гордости. Компания Baker Hughes, специализирующаяся на энергетических технологиях, применяет аддитивное производство (АП) для изготовления деталей, работающих в экстремальных условиях. Однако, с недавнего времени в компании поставили перед собой более амбициозную цель: наладить повторяемое производство сертифицированных запчастей по требованию, даже спустя годы после их разработки.
Большинство продуктов компании — промышленных клапанов и нефтегазового оборудования – предназначены для жестких условий эксплуатации. Эти детали должны быть прочными, износостойкими и выдерживать высокие температуры и давление. Например, в нефтяных скважинах они могут работать на глубине более 9000 метров. При этом требуются относительно небольшие партии — иногда всего несколько десятков деталей в год для конкретного бурового инструмента.
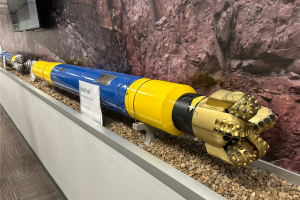
Такие объемы идеально подходят для аддитивного производства, и Baker Hughes уже достигла в этой сфере заметных успехов. Команда из 30 специалистов в Хьюстоне — инженеров, материаловедов и экспертов по контролю качества — разработала и сертифицировала ряд деталей.
Однако успешный запуск производства – это еще полдела. Ведь детали, созданные с помощью 3D-печати, должны изготавливаться с неизменной надежностью и точностью, даже если повторный заказ на них поступит через 5, 10 или более лет после разработки. В январе этого года команда Baker Hughes поделилась своим подходом к решению этой задачи — от разработки деталей и мониторинга с использованием искусственного интеллекта до программных решений, гарантирующих качество будущих 3D-печатных компонентов.
Оснащение для производства и разработки
В хьюстонском комплексе Baker Hughes, занимающем около 72 000 квадратных метров, команда аддитивного производства располагается на площади почти в 2 500 квадратных метров. Здесь размещены участки для металлической и полимерной 3D-печати, лаборатория материалов, а также офис.
Команда использует шесть лазерных L-PBF установок от Colibrium Additive (включая оборудование под брендами Concept Laser и GE), EOS и SLM Solutions. Каждая машина промаркирована по цвету в зависимости от используемого материала. Хотя в распоряжении команды есть различные порошки, основным сплавом все же остается Inconel 718 — он лучше всего подходит для коррозионно-активных сред в нефтегазовой отрасли.
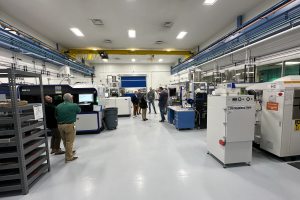
Для работ в сфере прямого подвода энергии и материала применяется проволочная WAAM система от Wolf Robotics (подразделение Lincoln Electric) и гибридный станок DMG MORI Lasertec 65, который совмещает газопорошковую наплавку и механическую обработку. Это оборудование используется не только для производства новых деталей, но и для ремонта, а также нанесения износостойких покрытий.
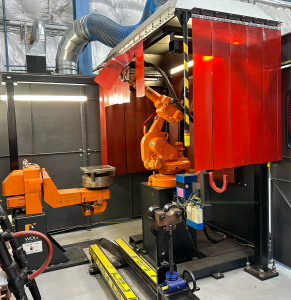
В полимерной лаборатории доступны технологии FFF, фотополимерной печати и струйного нанесения материалов. Как отмечает руководитель по работе с клиентами в сфере 3D-печати Михаил Анисимов, компания применяет практически все коммерчески успешные методы АП.
Инфраструктура предприятия также имеет оборудование для постобработки: установки для удаления порошка Solukon, смесители для регенерации материалов, проволочную ЭЭ, ленточнопильные станки, дробеструйные и полировальные машины, печь для термообработки Ipsen, а также промышленный компьютерный томограф Waygate Phoenix V|tome|x M300 для контроля качества.
Одной из ключевых причин внедрения АП в Baker Hughes стала консолидация цепочек поставок (об этом — далее), поэтому важно было охватить как можно больше этапов производства. Такой разнообразный парк оборудования обеспечивает скорость и гибкость не только в серийном выпуске, но и в разработке, которая составляет основную часть работы команды.
Перспективные направления для аддитивного производства
Baker Hughes работает во всех сегментах энергетики и промышленности, и её команда по АП поддерживает оба направления. Компания не только производит оборудование для клиентов, но и предлагает готовые решения под их нужды. В общем каталоге — десятки тысяч деталей, многие из которых можно выпускать с помощью 3D-печати.
В отличие от конкурентов, проводящих массовый аудит деталей для перевода на АП, Baker Hughes выбирает точечный подход. Как отмечает Трой Фальго, специалист по развитию бизнеса в сфере АП, команда фокусируется на запросах, отвечающих ключевым критериям:
- Сбои в поставках. Если традиционные методы производства затягивают сроки, АП позволяет быстро изготовить аналог без серьёзных доработок. Даже при более высокой себестоимости печати сокращение времени выпуска компенсирует затраты.
- Улучшение конструкций. АП даёт возможность модернизировать детали, повышая их эффективность.
- Инновационные решения. В некоторых случаях технология позволяет создавать принципиально новые продукты с уникальными свойствами, усиливая рыночные позиции компании.
Отличный пример – кавитационные стабилизаторы (VRT) для клапанов. Раньше их собирали из множества перфорированных пластин, что занимало до 9 месяцев с привлечением сторонних поставщиков. Переход на L-PBF-печать позволил создавать цельную деталь всего за 6 недель.
Но инновации на этом не остановились. На базе VRT была разработана серия EVO trim – клапанные компоненты со сложной внутренней геометрией, которые не просто гасят кавитацию, но и эффективно регулируют поток жидкости. Их уникальная конструкция с 32-64 разделительными каналами возможна только при аддитивном производстве.
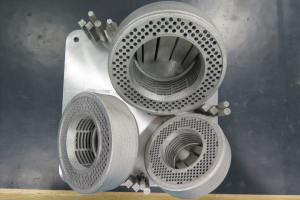
«Наша цель – создавать идеальные клапаны для конкретных условий, – объясняет Фальго. – АП позволяет точно проектировать гидродинамику и быстро вносить изменения, достигая характеристик, недоступных при традиционном производстве».
Успешные примеры применения аддитивного производства
Стабилизаторы кавитации VRT и EVO trim – примеры запчастей, которые Baker Hughes использует в сервисном обслуживании клиентов. Поскольку компания сама является и производителем, и оператором оборудования, процесс внедрения АП-деталей здесь проходит проще: Baker Hughes самостоятельно оценивает риски и принимает решения об их использовании.
Компания Baker Hughes добилась значительных результатов, внедряя 3D-печать в производство критически важных компонентов. Один из ярких примеров – лепестковая крышка для скважин, которая теперь изготавливается как единая деталь с гибкими зазорами между слоями. Это решение заменило сложный технологический процесс, включавший электроэрозионную обработку и сварку, и уже реализовано в 80 экземплярах.
Особого внимания заслуживает механический предохранитель. Его уникальная особенность – точное срабатывание при заданной нагрузке для защиты скважинного оборудования – стала возможна только благодаря АП, поскольку традиционная фрезеровка не обеспечивала необходимых характеристик материала.
Значительный прорыв достигнут в производстве буферных трубок. Вместо семи отдельных спаянных элементов теперь используется цельная металлическая конструкция со встроенными гидравлическими каналами, что существенно повысило надежность изделия.
Еще одним инновационным решением стали экраны и фильтры с интегрированными конформными ребрами жесткости. Эти напечатанные элементы предотвращают деформацию, обеспечивают равномерный износ рабочих слотов и исключают образование «путей наименьшего сопротивления» для абразивных частиц, что особенно важно при работе с песчаными смесями.
«Мы полностью отвечаем за качество этих деталей, – отмечает Хуан Карлос Флорес, исполнительный директор по передовым производственным технологиям. – Такой уровень ответственности ускоряет внедрение аддитивных компонентов внутри компании.»
«Но, когда речь заходит о серийных изделиях для рынка, процесс усложняется – здесь мы вынуждены действовать более осторожно», – добавляет он.
Преодоление барьеров: стандарты и уровень готовности технологий
Несмотря на соответствие отраслевым стандартам вроде API 20S для АП в нефтегазовой сфере, клиенты часто предъявляют дополнительные требования. Для серийных изделий обычно ожидается уровень готовности технологии (TRL) не ниже 8, подразумевающий успешные полевые испытания.
На текущий момент большинство аддитивных компонентов Baker Hughes находятся на более ранних стадиях развития. Лишь стабилизаторы кавитации VRT достигли TRL 8, тогда как разрабатываемый с 2021 года коллектор остановился на TRL 6. Как отмечает Трой Фальго, продвижение менее зрелых решений требует убедительной аргументации:
«Необходимо демонстрировать клиентам существенное улучшение производительности или снижение затрат, чтобы компенсировать более низкий TRL. Это сложная задача, ведь аддитивные технологии фундаментально отличаются от традиционных методов – мы фактически создаём материал в процессе производства, а не работаем с готовыми свойствами».
Однако материалы – лишь один аспект контроля качества. Baker Hughes реализует комплексный подход, тщательно документируя каждый этап производства: от отбора металлического порошка до настройки оборудования и поддержек.
«Данные – краеугольный камень нашей системы качества, – подчёркивает Фейсал Икбал, руководитель цифрового направления. – Мы гарантируем клиентам абсолютную прозрачность всех производственных процессов».
«Золотые файлы»: ключ к повторяемости
Baker Hughes сделала прозрачность и управление данными ключевыми элементами своей стратегии в аддитивном производстве. Внедрение платформы Oqton для управления производственными процессами революционно изменило работу с информацией – время генерации отчетов сократилось с 10 дней до нескольких минут, а клиенты получили прямой доступ к данным о своих заказах.
Специфика Baker Hughes требует особого подхода к данным. В отличие от массового производства, компания работает с небольшими партиями – иногда всего несколько тысяч деталей в год. Производственные линии могут неделю выпускать фильтры, которых хватит на годы использования, а затем переключиться на редкую модификацию VRT. Добавляет сложностей и привлечение сторонних подрядчиков. Как обеспечить идентичность деталей, выпущенных с интервалом в несколько лет?
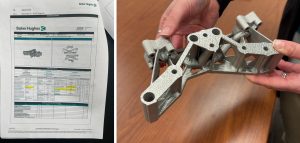
Ответом стала разработка комплексных цифровых досье, содержащих всю необходимую информацию для точного воспроизводства:
- Материальные спецификации и параметры печати.
- Протоколы постобработки и контроля качества.
- Полный набор данных в системе Oqton.
Любые изменения (поставщик, дизайн, ПО) требуют полной переквалификации изделия.
Компания отошла от традиционной практики, квалифицируя не отдельные детали, а целые платформы сборки – будь то два крупных компонента или сотня мелких. Это опровергает распространенный миф об отсутствии минимального заказа в АП. Например, фильтр, сертифицированный партией в 25 единиц, нельзя произвести в количестве 20 без повторной квалификации.
«Мы сертифицируем конкретное расположение на платформе, и оно должно строго повторяться, – поясняет Флорес. – Это дает нам полную определенность при повторном производстве».
Такой системный подход обеспечивает беспрецедентный уровень повторяемости – критически важный фактор для внедрения АТ в ответственных отраслях промышленности.
Следующий этап: распределённое производство под контролем ИИ
Параллельно с разработкой новых продуктов команда Baker Hughes работает над повышением надежности процесса 3D-печати. В сотрудничестве с Oqton компания создает собственный инструмент на основе искусственного интеллекта для мониторинга L-PBF. Модель обучена на библиотеке из 7 миллионов изображений аномалий, возникающих во время печати, и уже сейчас отслеживает процесс в реальном времени. В прошлом году система наработала 14 000 часов, выявляя такие проблемы, как коробление деталей или ошибки ракеля. В итоге для этого не требуется дополнительного оборудования – промышленные 3D-принтеры уже оснащены камерами по умолчанию.
Пока ИИ выполняет функции наблюдателя и архивиста. При обнаружении аномалий он отправляет уведомления операторам, которые принимают решение: остановить печать всей платформы или только проблемных деталей. В будущем система, возможно, сможет действовать автономно, гарантируя качество без вмешательства человека.
Однако главная цель разработки – обеспечить единые стандарты производства как внутри Baker Hughes, так и у внешних поставщиков. Сейчас 99% АП-деталей компания производит самостоятельно, но мощности ограничены. По мере роста каталога 3D-печатных компонентов часть заказов будет передаваться подрядчикам — и ИИ станет ключом к идентичности деталей, изготовленных на стороне.
Пока распределённое производство остается экспериментом. Принтеры в Хьюстоне работают стабильно, но не на полную загрузку, что даже удобно: всегда есть ресурсы для тестирования новых деталей.
Объёмы, однако, растут. Baker Hughes уже разработала более 1 000 АП-компонентов, выпускаемых партиями от нескольких штук до сотен. В общей сложности более 10 000 напечатанных деталей уже используются в работе. Компания готовится к будущему, где любой из этих элементов можно будет изготовить по требованию быстро и без потери качества.
«Наша цель – локализованное производство у конечного пользователя», – заключает Трой Фальго.
В итоге с помощью ИИ и «золотых файлов» Baker Hughes создает систему, в которой география не будет препятствием для надежных поставок.