Терморегулирование и инновационные материалы
Современные технологии терморегулирования и аддитивного производства меди открывают новые горизонты в создании высокоэффективных систем охлаждения и теплопередачи. Инновационные материалы и методы обработки позволяют достичь рекордных показателей теплопроводности, долговечности и энергоэффективности. В этой части мы рассмотрим ключевые разработки в области терморегулирования, включая передовые теплообменники, алмазно-медные композиты, графен-модифицированные порошки и технологию холодного напыления.
Теплообменники нового поколения
Компании Addtoshape S.r.L и CoolestDC представили революционные решения в производстве теплообменников с использованием аддитивных технологий. Addtoshape разработала биметаллические медные теплообменники с бионическими каналами охлаждения и интегрированными температурными датчиками. Эти устройства на 40% компактнее традиционных аналогов и демонстрируют на 35-40% более высокую тепловую эффективность. CoolestDC совместно с EOS создала интегрированные охлаждающие пластины для центров обработки данных, обеспечивающие температурную стабильность с отклонением всего ±0,5°C. Эти решения снижают энергопотребление на 15-20% и увеличивают плотность оборудования на 50-70%, что делает их идеальными для высоконагруженных серверных стоек и силовой электроники.
Алмазно-медные композиты
Прорывная разработка Харбинского технологического института — алмазно-медные композиты — демонстрирует теплопроводность до 700 Вт/(м·К), что почти вдвое превышает показатели чистой меди. Эти материалы сочетают в себе высокую теплопередачу с низким коэффициентом теплового расширения (≤10×10⁻⁶ K⁻¹), что критически важно для аэрокосмической техники и электроники. Технология включает струйное нанесение алмазного порошка с медным связующим и последующее спекание, что позволяет создавать сложные бионические структуры с интегрированными теплоотводами. Применение таких композитов в космических аппаратах, процессорных системах охлаждения и термоядерных установках открывает новые возможности для управления тепловыми потоками в экстремальных условиях.
Графен-модифицированные порошки
Совместные исследования Уппсальского университета и Graphmatech привели к созданию графен-модифицированных медных порошков, которые кардинально меняют подход к лазерной 3D-печати. Покрытие частиц порошка графеном толщиной 10-50 нм снижает отражательную способность меди с 95% до 28% для ИК-лазеров, что значительно улучшает качество плавления. Детали, напечатанные из таких порошков, обладают плотностью 99,2-99,5% и теплопроводностью 410 Вт/(м·К). Эти материалы особенно востребованы в электронике для производства теплоотводящих подложек и 3D-печатных шин питания, а также в аэрокосмической отрасли для создания сопловых вкладышей и систем охлаждения двигателей.
Холодное напыление для ремонта
Технология холодного газодинамического напыления (ColdSpray) меди, разработанная Plasma Giken, предлагает уникальный метод ремонта и модернизации металлических деталей без термического воздействия. Частицы меди напыляются со скоростью 300-1200 м/с при температуре 30-500°C, формируя слои с прочностью 90-110% от основного металла. Этот метод исключает деформации и коррозию, характерные для традиционной сварки, и сокращает время ремонта в 3-5 раз. Применяется для восстановления посадочных поверхностей, уплотнительных участков и создания биметаллических деталей в аэрокосмической, энергетической и транспортной отраслях. Например, ремонт турбинных лопаток или коленвалов с использованием этой технологии увеличивает их срок службы в 2-3 раза.
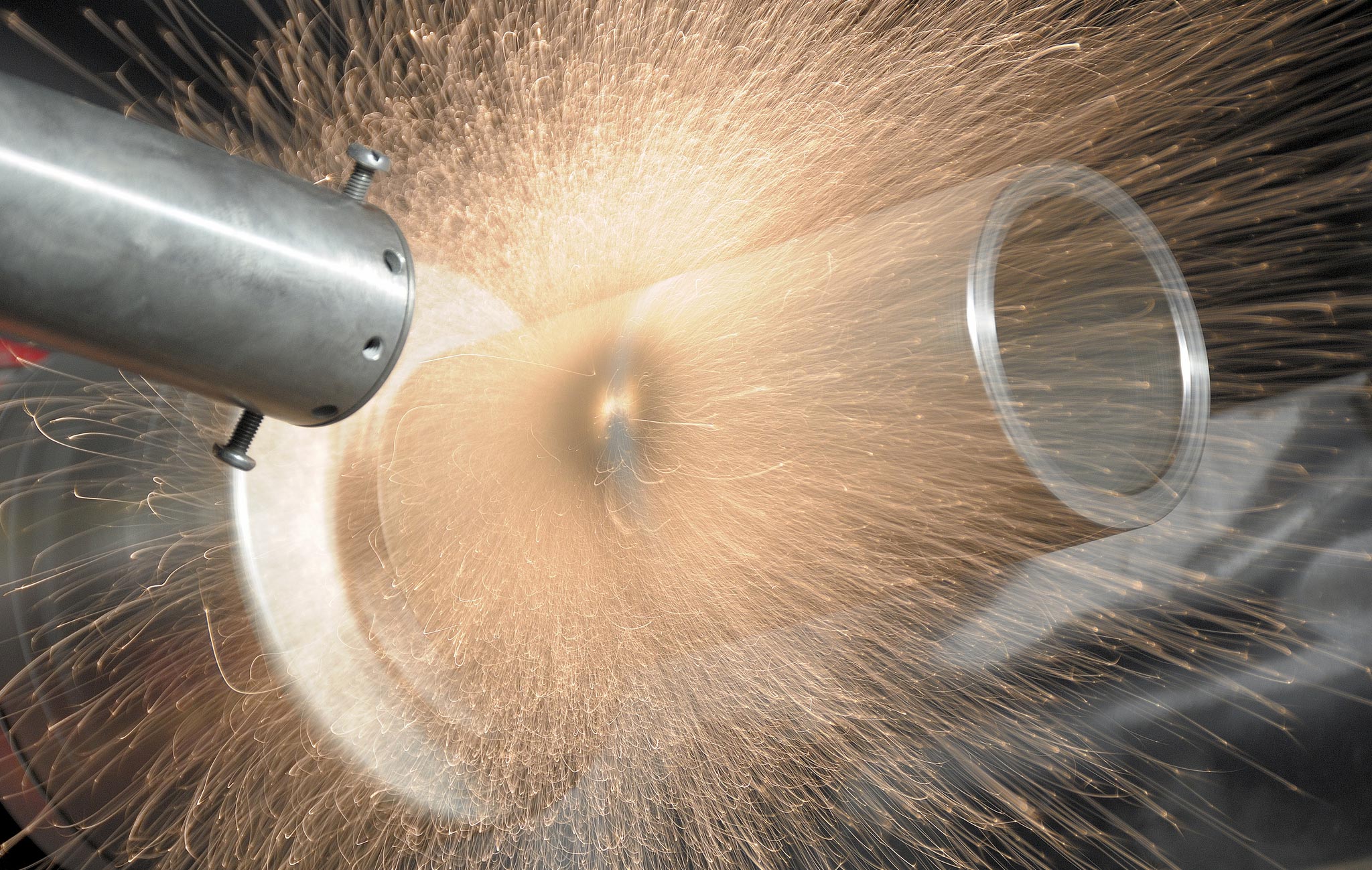
Инновации в области терморегулирования и материаловедения, такие как алмазно-медные композиты и графен-модифицированные порошки, задают новые стандарты эффективности и надежности. Технологии холодного напыления и аддитивного производства теплообменников демонстрируют, как современные методы обработки меди могут решать сложные инженерные задачи. Эти разработки не только улучшают эксплуатационные характеристики устройств, но и способствуют устойчивому развитию, снижая энергопотребление и материальные отходы. Будущее терморегулирования — за интегрированными, многофункциональными решениями, созданными с учетом экстремальных условий и требований цифровой эпохи.
Совершенство и дефекты в аддитивном производстве меди
Аддитивное производство меди представляет собой сложный технологический процесс, где малейшие отклонения могут привести к критическим дефектам. Особенно это актуально для аэрокосмической отрасли, где требования к качеству деталей исключительно высоки. Основные проблемы включают различные виды пор, трещин и структурную неоднородность.
Как отмечают эксперты, обработка чистой меди сопряжена с дополнительными сложностями. «При печати чистой медью требуется значительный подогрев плиты построения, — поясняет эксперт Константин Бабкин. — Однако при температурах выше 100°C начинается активное спекание и окисление порошка даже при минимальном содержании кислорода в защитной атмосфере. Это неизбежно приводит к снижению электропроводности – ключевого свойства меди».
«На практике наибольшее применение для L-PBF-технологии находят малолегированные бронзы с высокой тепло- и электропроводностью (содержащие около 99% меди). Опыт синтеза малолегированных бронз показывает практическую применимость ИК-лазеров — стандартного оборудования для L-PBF как в России, так и за рубежом. Критическим параметром является температура подогрева плиты построения: её изменение даже на 50°C приводит к резкому увеличению дефектов (пор и несплавлений) в структуре материала. Экономический аспект также играет важную роль: при нагреве до 150–200°C происходит интенсивное окисление порошка, контактирующего с деталью. Для повторного применения таких оборотных порошков задача отделения окисленных частиц от годных к повторному применению представляется крайне сложной. По факту же, печать с относительно высокими температурами подогрева плиты построения (в зависимости от плотности заполнения плиты построения) часто ограничивается однократным применением металлопорошковых композиций из-за невозможности отделения годного порошка», — делится опытом Алексей Мазалов, генеральный директор АО «ЦАТ».
Inconel 718 и GRCop-42
Для преодоления этих ограничений инженеры разрабатывают специализированные сплавы. Никелевые составы типа Inconel 718 демонстрируют исключительную термостойкость, титановые сплавы сочетают легкость и прочность, а медные композиции вроде GRCop-42 обеспечивают превосходное терморегулирование.
Термическая обработка играет ключевую роль в достижении оптимальных характеристик. В то время как никелевые сплавы приобретают дополнительную прочность за счет пластичности, алюминиевые составы становятся более гибкими. Ряд медных сплавов (например, GRCop) сохраняет уникальный баланс прочности и термостойкости, оставаясь устойчивыми к многократным тепловым нагрузкам.
Таким образом, аддитивное производство меди требует тщательного контроля всех параметров процесса — от состава защитной атмосферы до режимов термической обработки. Только комплексный подход позволяет минимизировать дефекты и получить детали, соответствующие самым строгим промышленным требованиям.
Влияние ИИ на проектирование и управление качеством в аддитивном производстве меди
Искусственный интеллект перестал быть вспомогательным инструментом — он стал ключевым фактором преобразований в работе с медью. В авангарде этой революции компания LEAP 71 (ОАЭ), бросившая вызов традиционному инженерному процессу. Их вычислительная модель Noyron заменила ручное CAD-моделирование автономным генеративным проектированием. Задавая параметры, — тягу, тип топлива, термонагрузки, ИИ создает оптимизированную конструкцию за минуты вместо месяцев. Например, жидкостный ракетный двигатель тягой 5 кН был спроектирован ею за 2 недели, а клиновоздушный (от англ. aerospike, аэроспайк) — за 3 недели.
Для меди, капризной и требовательной, это прорыв: Noyron создает системы охлаждения с каналами переменного сечения до 0,8 мм в камерах сгорания из CuCrZr, где керосин циркулирует, отводя тепло от стенок, нагретых до 3000°C. В двигателе аэроспайк ИИ решил проблему перегрева центрального шипа, спроектировав сеть микроканалов, по которым жидкий кислород снижает температуру с 3500°C до 250°C на поверхности. Выбор CuCrZr здесь не случаен — сплав сочетает теплопроводность (~330 Вт/(м·К)), прочность (450 МПа) и технологичность печати на оборудовании EOS M290.
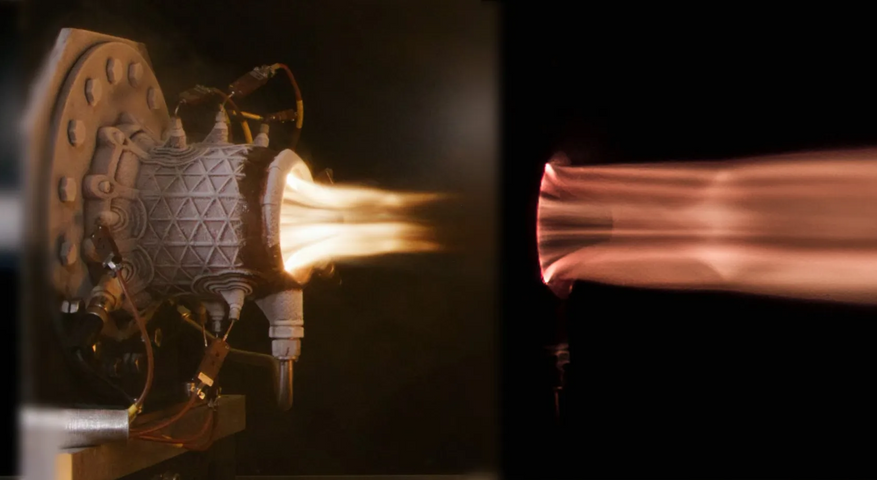
Испытания 2024
Испытания в июне 2024 года в Великобритании стали триумфом подхода: данный двигатель проработал 11 секунд на жидком кислороде и керосине, подтвердив стабильность тяги с первой попытки. Данные тестов автоматически загружались в Noyron, запустив цикл самообучения для корректировки будущих конструкций. Это замкнуло петлю «проектирование — производство — верификация», сократив путь от чертежа до огневых испытаний с месяцев до недель.
Но ИИ меняет не только проектирование — он трансформирует контроль качества на молекулярном уровне. Системы компьютерного зрения на базе сверточных нейронных сетей CNN (от англ. Convolutional Neural Networks) анализируют видео печати в реальном времени, выявляя дефекты слоев: нитеобразные структуры из-за неточностей температуры, отклонения в выкладке порошка или сплавлении меди. Датчики в установках L-PBF отслеживают стабильность плавления, предупреждая о риске пористости в медных сплавах. Алгоритмы научились прогнозировать деформации меди при нагреве платформы свыше 100°C и корректировать параметры «на лету», минимизируя окисление порошка. А инструменты с проверкой печати могут автоматически анализировать 3D-модель на совместимость с медными сплавами: они проверяют минимальную толщину стенок (от 0,3 мм), углы свеса, термоусадку, рекомендуя постобработку, — например, горячее изостатическое прессование (HIP) для GRCop-84, повышающее плотность до 99,5%. Для повторного использования порошка ИИ оценивает уровень окисления частиц CuCrZr, сокращая отходы на 15–30% и экономя до $50/кг.
Итоги испытаний
Ключевые прорывы здесь — в устранении «слепых зон» производства. Традиционный подход требовал 3–6 месяцев ручных итераций для проектирования; ИИ сокращает его до 2–3 недель. Визуальный осмотр деталей после печати снижал брак на 20–30%; мониторинг слоя CNN повысил эффективность до 40%. Проблема непроплавления (LOF-пор), характерная для ИК-лазеров из-за отражения от меди, при использовании синих лазеров с их высоким поглощением (65-70%) существенно снижается.
Гибридные ИИ-системы объединят генеративный дизайн (как Noyron) с контролем качества в реальном времени, сжимая цикл «проектирование — испытания» до одной недели. Цифровые двойники медных компонентов — теплообменников, сопел ракетных двигателей — будут предсказывать износ на основе данных испытаний, аналогичных тем, что получены для GRCop-84. А ИИ-стандартизация порошков решит проблему разброса свойств материалов: алгоритмы прогнозируют поведение медных композиционных материалов (графен-Cu, алмаз-Cu) при печати, гарантируя стабильность параметров от партии к партии.
ИИ не просто оптимизирует процессы — он создает инженерный язык, на котором медь, древний и капризный металл, обретает новую выразительность. Широкий спектр применений — от создания сложных криволинейных каналов в ракетных двигателях до изготовления микрорадиаторов с идеальной геометрией — это стало уже нашей реальностью, выкованной алгоритмами.
Заключение
Аддитивное производство меди — это не просто технологический прорыв, а настоящая революция, которая перекраивает границы возможного. Медь, когда-то капризный металл, сопротивлявшийся традиционным методам обработки, превратилась в материал будущего, открывающий двери для инноваций в электронике, энергетике, аэрокосмической и других ведущих и наукоемких отраслях. Зеленые и синие лазеры стали тем волшебным ключом, который позволил раскрыть её потенциал, создавая детали с недостижимой ранее точностью и эффективностью.
Но самое удивительное — это даже не сами технологии, а то, как они меняют наше представление о производстве. Где раньше требовались десятки деталей и сложные сборки, теперь появляются единые, генеративно оптимизированные конструкции. Где когда-то были ограничения, теперь — свобода для инженерной мысли. Медь, многовековой спутник человечества, обретает новую жизнь, становясь материалом для космических двигателей, теплоотводов и энергоэффективных электромоторов.
Будущее уже здесь, и оно блестит медным отливом. Остается только задаться вопросом: какие ещё горизонты откроются, когда мы научимся полностью понимать этот удивительный металл? Одно можно сказать наверняка — путь вперёд будет таким же ярким, как луч лазера, плавящий медь в нечто совершенно новое.
Ознакомьтесь с нашими другими статьями, по этой теме:
Введение и рынок аддитивного производства меди (часть 1)
Технологии аддитивного производства меди (часть 2)
Зеленые и синие лазеры в аддитивном производстве меди (часть 3)