Проект LeiMot
Современные бензиновые и дизельные двигатели для легковых автомобилей, выполненные полностью из алюминия, оптимизированы по стоимости и весу с использованием новейших традиционных технологий производства.
В последние годы соотношение веса и мощности этих двигателей стало асимптотическим. Оно приближается к 1,1 кг/кВт для трех- и четырехцилиндровых двигателей [1].
Такое поведение отражает баланс между свойствами материала, профилем нагрузки и использованием конструкции при заданных граничных условиях производства двигателя.
Это показывает, что дальнейшего существенного снижения веса при использовании традиционных методов производства ожидать не приходится. Переход производственного процесса на метод лазерного наплавления в порошковом слое (LPBF/SLM) позволяет еще больше снизить вес при использовании тех же или аналогичных материалов и профилей нагрузки.
В рамках проекта LeiMot (Leichtbau Motor) (облегченный мотор, от нем. Leicht – легкий – прим.ред.), который спонсируется Федеральным министерством экономики и технологий Германии (BMWi) под руководством FEV Europe, были разработаны головка блока цилиндров и картер двигателя для процесса LPBF.
Дизельный агрегат был выбран из-за его более высокой механической грузоподъемности (Volkswagen 2,0-l TDI, EA288 evo). Компоненты были разработаны в соответствии с концепцией замены.
Для компонентов, изготовленных с использованием аддитивного производства (далее АП), был использован порошок AlSi10Mg, который является наиболее часто используемым алюминиевым сплавом в АП. Более высокая степень свободы при проктировании конструкции для АП была использована не только для снижения веса, но и для улучшения работы двигателя.
При разработке концепции двигателя LeiMot граничные условия АП для проектирования головки блока цилиндров и картера последовательно соблюдались от концепции до производственного процесса, включая опорные конструкции, ориентацию и последующую обработку [2].
Кроме того, в качестве цели было определено использование процесса термореактивного литья под давлением. Чтобы использовать его разумно, необходимо было разработать подходящую концепцию картера. Доступным материалом является волокнистый композитный пластик (FRP) на основе фенольной смолы, армированной стекловолокном.
Концепция компонентов
Первоначально головка блока цилиндров и картер были разобраны на их функции. Таким образом, каждая функция может быть проанализирована с самого начала, а их компоновка может быть адаптирована в соответствии с заданными требованиями. Одним из основных требований концепции была перекрестная совместимость между головкой блока цилиндров LeiMot и базовым картером Volkswagen. Кроме того, необходимо было сохранить важные интерфейсы и компоненты эталонного двигателя, особенно коленчатый вал и клапанный механизм, а также компоненты газообмена.
При соответствующей методологии проектирования такие функции, как охлаждение, смазка и обмен нагрузками, могут быть выполнены из материала с толщиной стенок 2 мм и даже ниже. Стенки и перемычки решетчатых конструкций также могут быть спроектированы с толщиной значительно ниже 2 мм. По сравнению с традиционными процессами литья, это позволяет использовать стенки различной толщины в соответствии с нагрузкой, не создавая связанных с процессом недостатков в конструкции.
Головка блока цилиндров
Вначале основное внимание уделялось общей конструкции головки блока цилиндров для безопасной эксплуатации в зонах с высокими механическими нагрузками. Изгибающая нагрузка возникает в основном в результате самого процесса сгорания, в то время как весь двигатель подвергается нагрузкам на кручение.
Результатом этого анализа стало сочетание двутавровой балки (IPB) со встроенным закрытым профилем для конструкции, которую также можно найти в окончательном проекте головки блока цилиндров, Рис. 1 [3].
Новая головка блока цилиндров имеет вес 8,5 кг, что на 22% легче эталонной головки блока цилиндров.
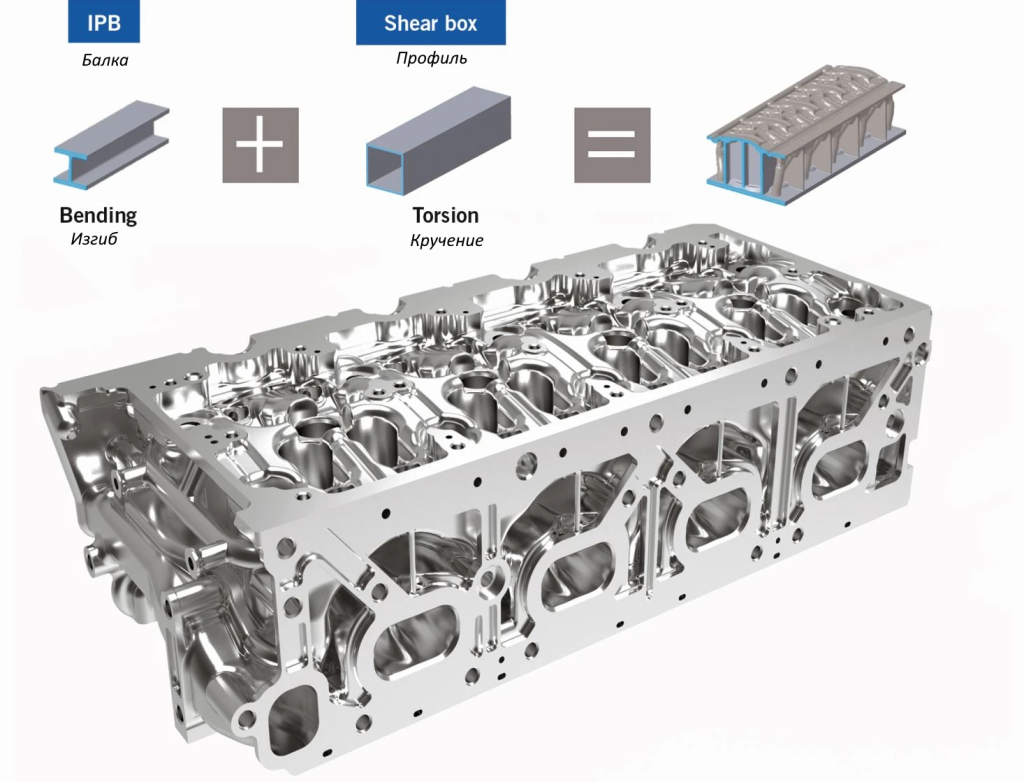
Рис.1 – Конструктивная схема головки блока цилиндров (© FEW)
Блок цилиндров и опорная плита
Картер концептуально оснащен горизонтальными опорными конструкциями между объемными головками. Открытые конструкции получили повышенную жесткость за счет поперечных ребер жесткости рядом с другими локальными функциональными элементами, такими как каналы для воды или масла, которые также способствуют жесткости. Кроме того, переборки оснащены облегченными трубообразными конструкциями, которые закрывают балансировочные валы по всей длине картера.
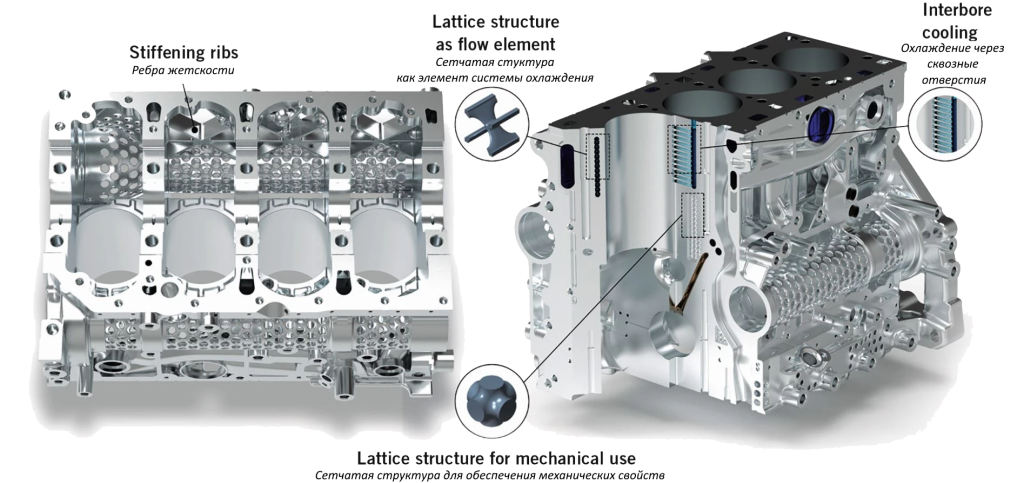
Рис.2 – Блок цилидров проекта LeiMot (© FEV)
роме того, конструкция с глубокой юбкой эталонного двигателя была изменена на конструкцию с короткой юбкой и алюминиевой опорной плитой по соображениям веса и жесткости.
Алюминиевая опорная плита заменяет тяжелые стальные крышки основных подшипников, одновременно придавая жесткость нижней части картера. Это приводит к снижению веса примерно на 2 кг по сравнению с аналогичной секцией картера со стальными крышками основных подшипников.
Основные траектории нагрузки были определены с помощью топологической оптимизации, которая позволила реализовать полости или соответствующие решетчатые конструкции во внешних областях с низким напряжением, таких как переборки или фланцы головки блока цилиндров, Рис. 2. Эти исследования являются основой граничной оптимизации под воздействием тепловых и механических нагрузок. В ходе проекта будут проведены дальнейшие исследования.
Конструкция головки блока цилиндров и опорной плиты картера были подтверждены с помощью CAE. Применение критериев серийного производства было обязательным.
Чрезвычайно легкая конструкция требует точного знания свойств материала во время компоновки и расчета. Из-за его особой микроструктуры существуют значительные различия между механическими свойствами деталей, изготовленных с использованием АП, и классических (серийных) литых деталей [4]. Поэтому были напечатаны тестовые образцы, чтобы исследовать анизотропные механические свойства при различных температурах. Полученные результаты затем были использованы в расчетах.
Использование решетчатых/сетчатых структур для обеспечения механических свойств, Рис. 2, значительно увеличивает сложность модели конечных элементов (Finite Elements, FE), что приводит к очень длительному времени расчета. По этой причине решетчатые структуры в глобальной модели были заменены упрощенными элементами, которые представляют те же механические свойства, что и используемые решетчатые структуры.
Охлаждение
Концепция охлаждения с поперечным потоком была разработана для равномерного охлаждения каждого цилиндра. Цель системы охлаждения головки блока цилиндров – обеспечить целенаправленное охлаждение каждого цилиндра при одновременном уменьшении объема воды, что приводит к сокращению продолжительности прогрева из-за меньшей тепловой инерции при холодном запуске. Поэтому вводятся отдельные трубки определенного диаметра (охлаждение артерий), охватывающие кольца седла клапана и вал инжектора, Рис. 3. Благодаря этому вводимое тепло отводится непосредственно в горячих точках и транспортируется с высокой скоростью потока. Положительным побочным эффектом отдельных труб является увеличение жесткости камеры сгорания по сравнению с водяной рубашкой большего объема.
Для обеспечения достаточного охлаждения вокруг выпускных отверстий при меньшем объеме охлаждающей жидкости была использована водяная рубашка толщиной 5 мм, Рис. 3. Кроме того, такая компоновка обеспечивает достаточное охлаждение вокруг высоконагруженных направляющих клапанов со стороны выпуска. Сравнительный термический анализ FE показал, что температуру в зоне камеры сгорания головки блока цилиндров можно снизить до 40 °C с помощью того же водяного насоса, Рис. 4. Чтобы вернуть температуру стенок камеры сгорания к исходному уровню, можно уменьшить расход и, следовательно, мощность насоса. Даже при снижении общего расхода охлаждающей жидкости через головку блока цилиндров и картер на 40% максимальная температура стенок по-прежнему намного ниже, чем у эталонного двигателя с обычной водяной рубашкой
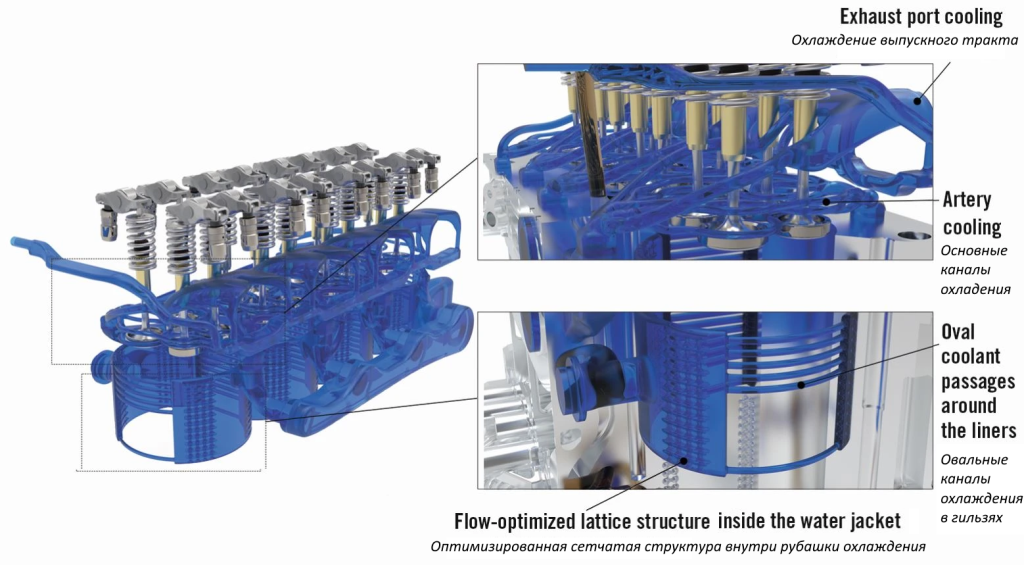
Рис.3 – Водяная рубашка LeiMot (© FEV)
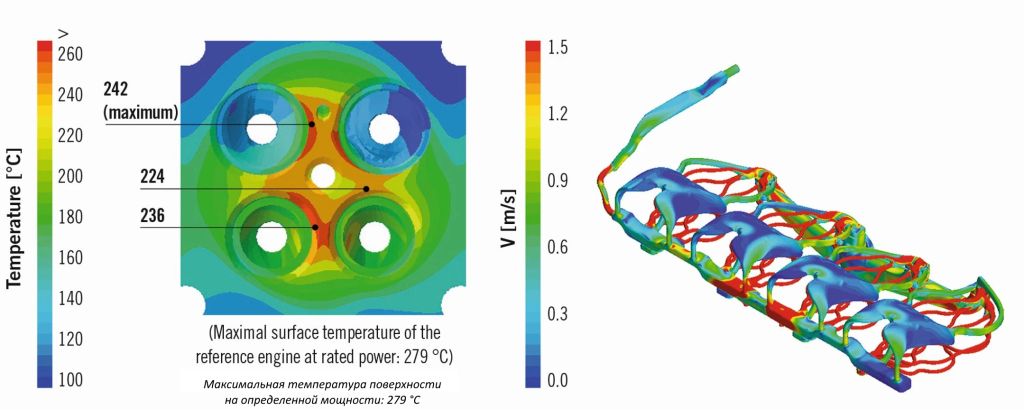
Рис.4 – Распределение температуры на поверхности камеры сгорания (слева) и скорости потока внутри водяной рубашки головки блока цилиндров (справа) без снижения расхода при номинальной мощности ( © FEV)
Для улучшения охлаждения картера и достижения равномерного распределения температуры по цилиндрам, в качестве промежуточного охлаждения между цилиндрами были реализованы овальные охлаждающие каналы размером 2 × 3 мм (ширина × высота). Кроме того, в водяную рубашку встроены оптимизированные для потока решетчатые конструкции, Рис. 3.
Решетчатые конструкции увеличивают площадь теплопередачи, улучшают направление потока охлаждающей жидкости и жесткость гильзы цилиндра. Улучшенное охлаждение гильзы цилиндра за счет включения охлаждения между отверстиями в сочетании с опорной решетчатой конструкцией приводит к относительно равномерному профилю деформации гильзы во время работы двигателя и, следовательно, создает потенциал для снижения трения и продувки.
Масляный контур
Основной акцент в концепции масляного контура был сделан на снижении потерь давления, чтобы обеспечить преимущества при нормальной эксплуатации и при холодных пусках.
АП позволяет реализовать новую компоновку масляных каналов без каких-либо острых краев, Рис. 5. Масляные каналы диаметром от 3 до 8 мм внутри головки блока цилиндров и картера были спроектированы для 3D-печати. Использование изогнутых каналов и плавных переходов поперечного сечения в системе металлической печати позволяет снизить потери давления примерно на 22%.
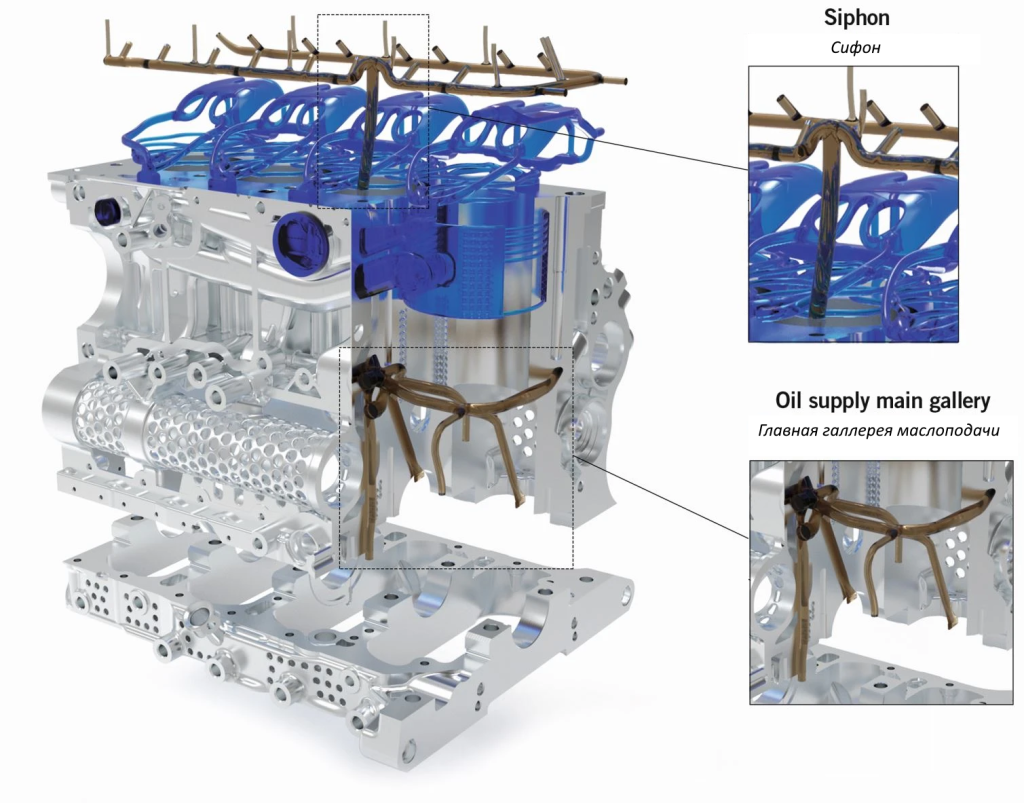
Рис.5 – Система смазки ( © FEV)
Подача масла в компоненты клапанного механизма улучшена благодаря новой конструкции магистрального трубопровода подачи и главной галереи внутри головки блока цилиндров. Они препятствуют сливу масла в нерабочее время благодаря встроенному сифону, Рис. 5.
Первоначальные топологические исследования показали, что картер с полыми перегородками обладает достаточной конструктивной жесткостью. Конструкция была соответствующим образом скорректирована таким образом, чтобы полые части картера можно было использовать в качестве каналов возврата масла.
Изоляция выпускного отверстия
Свобода проектирования для АП позволяет создавать различные конструкции, пригодные для печати. Основной идеей показанного изолированного выпускного отверстия было целенаправленное расположение элемента теплоизоляционной решетки, снижающего тепловой поток, который можно комбинировать с воздушным зазором, Рис. 6.
Это приводит к уменьшению теплового потока от выхлопных газов в охлаждающую жидкость двигателя. Данная система снижает тепловой поток примерно на 5% при номинальной мощности. Это обеспечивает более короткий период прогрева системы доочистки выхлопных газов и более высокую температуру на входе в турбину.
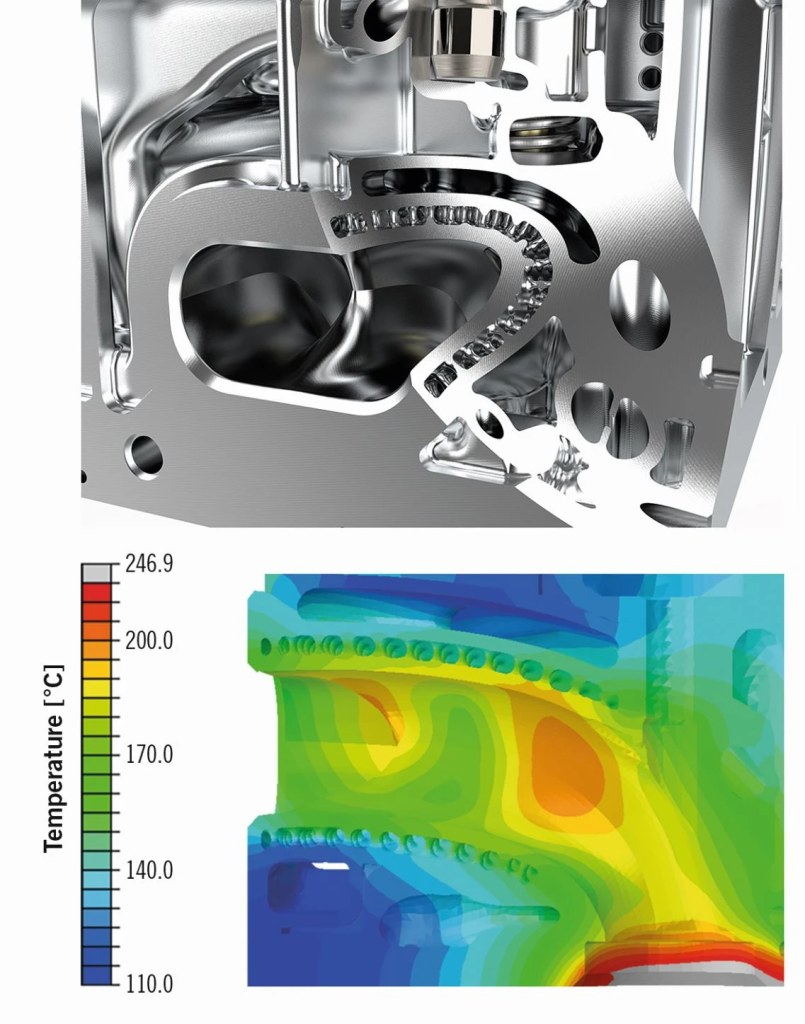
Рис.6 – Система изоляции выпускного отверстия ( © FEW)
Распределение конструкции стойки было оптимизировано с целью обеспечения максимальной температуры стенок выпускного отверстия в пределах материала, обеспечивая при этом равномерное распределение температуры стенок по всему выпускному отверстию. Максимальная температура стенок достигает около 200 °C, что находится в пределах допустимых значений для материала.
Крышки головки блока цилиндров
В гибридной конструкции из алюминия и пластика боковые стенки впускной и выпускной частей картера были изготовлены партнером Fraunhofer ICT из высокопрочного композитного материала, армированного волокнами. Пластмассовые компоненты большого объема изготавливаются методом литья под давлением из формовочных смесей, армированных стекловолокном из фенольной смолы. Из-за его меньшей плотности, химической стойкости к маслу и гликолю, хороших механических свойств даже при высоких рабочих температурах и низкой ползучести в качестве материала был выбран термореактивный пластик [5].
Основное внимание уделяется облегченной конструкции с высокой степенью функциональной интеграции в конструкции боковых стенок из термореактивного материала. В дополнение к крашкам картера, в конструкции интегрированы каналы охлаждающей жидкости, насос охлаждающей жидкости с механическим приводом и масляный фильтр, маслоохладитель и модуль распределения охлаждающей жидкости.
Благодаря боковым крышкам, изготовленным из формовочных составов из фенольной смолы, армированной стекловолокном, картер LeiMot примерно на 15% легче по сравнению с полностью алюминиевым картером.
Для герметизации холодной стороны был использован клей на основе силикона. Благодаря более высокому относительному удлинению при разрушении по сравнению с другими клеями можно компенсировать различные характеристики термического расширения термореактивного пластика и алюминия.
Боковая крышка из термореактивного пластика с холодной стороны крепится непосредственно к картеру саморезами. Для улучшения характеристик NVH (Noise, Vibration, and Harshness прим. ред.) термореактивная крышка с горячей стороны (сторона выхода выхлопных газов) крепится к картеру с помощью виброизолирующих элементов. Эти элементы крепятся болтами к алюминию и удерживают термореактивную крышку прижатой к картеру с помощью эластомера. Для картера предусмотрено уплотнение из эластомерного профиля. Применение различных методов соединения с горячей и холодной стороны позволяет сравнить оба метода соединения на прототипе LeiMot. Используемые методы проверяются путем моделирования и предварительного тестирования.
Акустика
При эксплуатации двигателя возникает фундаментальная проблема, типичная для проектов с облегченным дизайном, из-за более высоких амплитуд колебаний локально более слабых конструктивных элементов.
Динамические расчеты конструкции показали, что требуется повышение жесткости картера при кручении и сдвиге. По этой причине оценки NVH проводились непрерывно и итеративно с учетом конструктивных аспектов и расчетов долговечности, начиная с первоначальной концепции двигателя [6].
Картер LeiMot имеет повышенное излучение над клапанной крышкой и масляным поддоном, где всегда происходит основное акустическое излучение двигателя внутреннего сгорания. Следует отметить, что новые боковые крышки картера не увеличивают звуковое излучение в воздухе.
Исследования показывают, что разница между отсоединенной и жестко прикрепленной крышкой незначительна. Выраженных резонансов возникнуть не может. Излучение клапанной крышки и масляного поддона остается доминирующим.
Преимущество в весе более чем на 21% контрастирует с повышением уровня шума на 2,3 дБ (А). Основные характеристики слегка повышаются за счет уменьшения веса (кручения). Благодаря ребрам жесткости между переборками и решетчатой трубчатой конструкции вокруг балансировочных валов дополнительный режим сдвига можно настроить таким образом, чтобы уровень на частоте 1100 Гц оставался в пределах полосы рассеяния.
Выводы и заключения
Новые методы производства, такие как LPBF (SLM), позволяют реализовать дополнительные возможности снижения веса. В рамках проекта LeiMot вес головки блока цилиндров и картера был снижен примерно на 21% по сравнению с новейшим 2,0-литровым дизельным двигателем Volkswagen EA288 evo.
В дополнение к снижению веса, проект LeiMot предлагает возможности для повышения эффективности за счет уменьшения мощности насоса охлаждающей жидкости и масляного насоса, уменьшения трения в группе поршень/гильза, снижения выбросов при холодном запуске и увеличения мощности турбины турбонагнетателя за счет изоляции выпускных отверстий.
В 2021 году планируется изготовить пять прототипов LeiMot и провести механические и термодинамические испытания.
Проект LeiMot способствует демонстрации конструктивных возможностей новых технологий производства. Кроме того, он должен вдохновить на новые методы разработки двигателей внутреннего сгорания и не только.
В краткосрочной и среднесрочной перспективе крупносерийные АП-компоненты, такие как те, что разработаны в рамках проекта LeiMot, пока не смогут конкурировать с традиционными методами производства в сегменте массового рынка. Сегодня аддитивное производство небольших компонентов уже внедрено вплоть до серийного производства в небольших количествах.
Традиционные технологии производства смогут извлечь выгоду из возможностей аддитивного производства. Возможным подходом было бы создание филигранных структур, как при охлаждении LeiMot, для песчаных стержней и внедрение их в обычный процесс литья. Еще одним способом могло бы стать использование в будущем гибридных решений, сочетающих аддитивное и традиционное производство.
Список источников:
[1] Bey, R.; Bick, W.: Advanced Light Weight Combustion Engine Concept for Passenger Car Application. Light Weight Composite Solution Conference, Gent, 2018
[2] Kranz, J.: Methodik und Richtlinien für die Konstruktion von laseradditiv gefertigten Leichtbaustrukturen. Hamburg, Technische Universität Hamburg-Harburg, Dissertation, 2017
[3] Büchau, N.; Bick, W.; Bey, R.; Rauschen, R.: Entwicklung eines Zylinderkopfs unter den Möglichkeiten der additiven Fertigung. 8th VDI-Fachtagung Ventiltrieb und Zylinderkopf, Würzburg, 2019
[4] Zygula, K.; Nosek, B.; Pasiowiec, H.; Szysiak, N.: Mechanical Properties and Microstructure of AlSi10Mg Alloy Obtained by Casting and SLM Technique. AGH University of Science and Technology, 2018
[5] Berg, L.: Phenolharzspritzgießen – Anwendungen in modernen PKW Antriebsstrangkomponenten. VDI Conference Hochleistungskunststoffe in der Anwendung, Berlin, 2017
[6] Nussmann, C.; Steffens, C.; Atzler, M.: Modern Tools and Methods for Low Noise Engine Development. ISMA Conference, Leuven, 2010