Японский автопроизводитель Honda изучает возможности 3D-печати для производства автомобилей, мотоциклов, мототехники, силовых установок, аэрокосмической техники и гоночных колясок. Недавно компания сообщила, что изучает, как технология лазерного сплавления порошка (LPBF) может “добавить новую ценность в производственные процессы”.
Глобальный автопроизводитель, расположенный в Минато, Токио, утверждает, что 3D-печать позволяет быстро и эффективно создавать сложные формы при меньших затратах, чем традиционные методы. Он также указал на потенциал “умных фабрик” 3D-печати, которые могут “значительно сократить процесс от разработки до массового производства”.
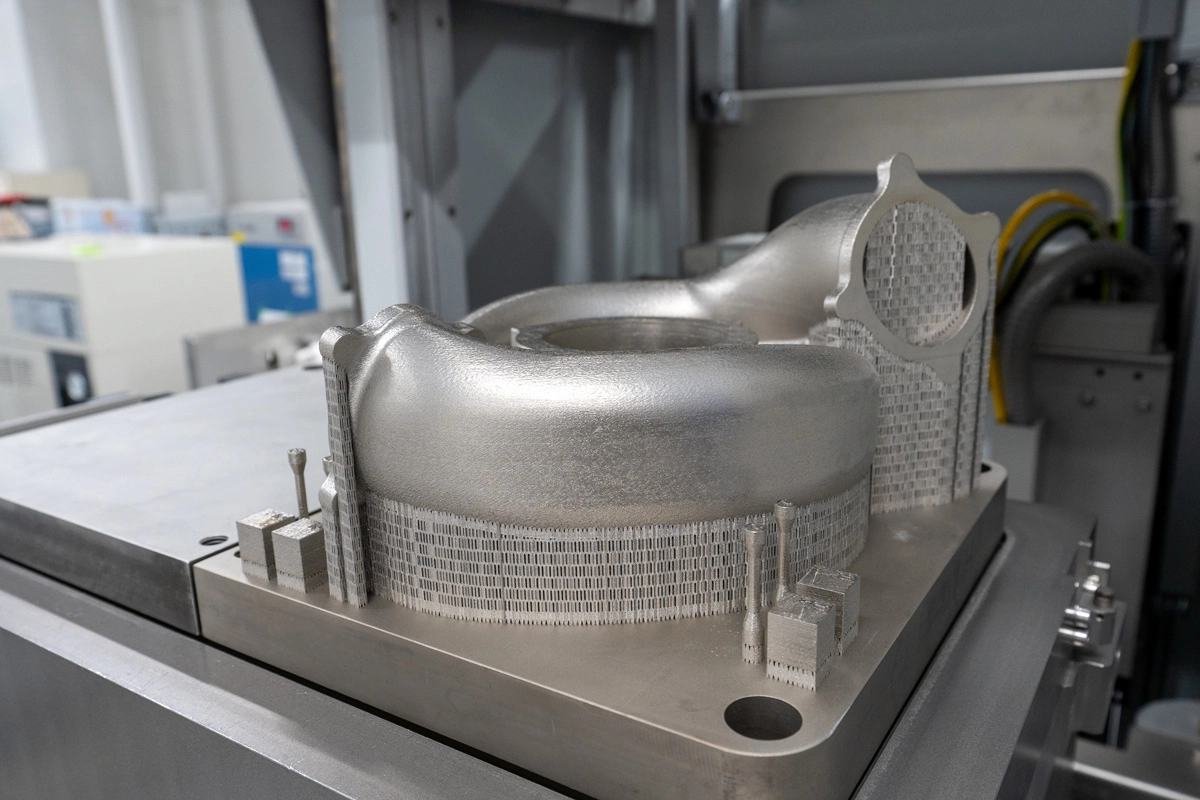
Примечательно, что Honda уже использует 3D-печать LPBF для производства компонентов автомобильных двигателей. К ним относятся поршни и корпуса турбин, используемые в болидах Oracle Red Bull Racing в Формуле-1. Компания также использует аддитивное производство из металлов для изготовления легких алюминиевых ручек, оптимизированных по топологии, для гоночных инвалидных кресел.
3D-печать металлом в компании Honda
Компания Honda стремится все больше внедрять аддитивное производство из металлов в свои разработки и производственные процессы. Она уже печатает металлические детали в домашних условиях с помощью технологии LPBF, включая системы от Nikon SLM Solutions.
Компания утверждает, что накопила опыт в области АП, оптимизируя параметры, регистрируя осаждение материала для оценки состояния плавления, а также контролируя температуру и мощность лазера. Технология моделирования процесса также используется для прогнозирования и смягчения возможных деформаций и повышения точности размеров деталей. Honda отметила, что 3D-печать металла позволяет ей изготавливать детали сложной формы, которые невозможно получить с помощью традиционных методов литья и ковки.
В 2019 году компания сотрудничает с Oracle Red Bull Racing, поставляя двигатели для их автомобилей Формулы-1. Аддитивное производство из металла помогло им быстро адаптироваться к изменениям спецификации и создавать сложные тонкостенные детали. Это, в свою очередь, сократило сроки изготовления и снизило затраты.
Гоночный гигант, в составе которого выступает действующий чемпион Формулы-1 Макс Ферстаппен, ранее использовал поршни, изготовленные методом алюминиевой штамповки. Honda перешла на 3D-печать LPBF, используя железный порошок для дополнительной прочности под давлением при сгорании. Хотя железо тяжелее алюминия, новые 3D-печатные геометрии позволили сделать конечные детали легче обычных аналогов.
Аналогичным образом, детали корпуса турбины команды Формулы-1 ранее изготавливались из инконеля, жаропрочного никелевого сплава, методом точного литья. Эти крупные компоненты имеют тонкие стенки, что приводило к проблемам с деформацией при традиционном производстве. 3D-печать корпусов, как сообщается, устраняет эти проблемы, позволяя Honda соответствовать строгим требованиям, снижая при этом затраты и сокращая время производства.
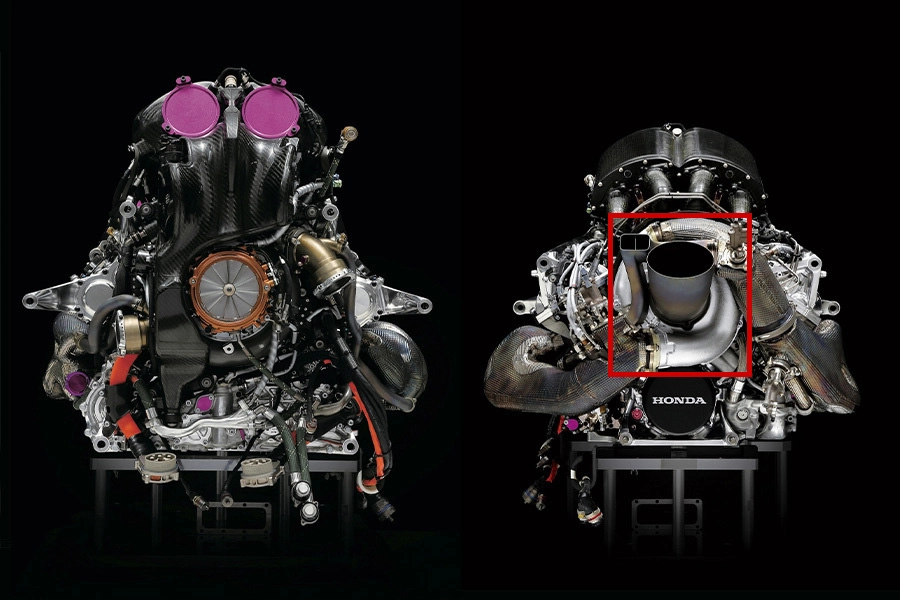
Технология аддитивного производства из металлов также используется для изготовления алюминиевых рулей для гоночных колясок Honda, также известных как “хэндциклы”. Используя 3D-печать, ведущая марка мотоциклов стремится снизить вес и повысить безопасность при столкновениях.
Оптимальная геометрия руля зависит от формы рук каждого спортсмена. Ранее эти детали изготавливались из сварных алюминиевых труб, что давало минимальные возможности для кастомизации. Чтобы решить эту проблему, Honda использовала оптимизацию топологии для создания более эргономичного компонента при минимизации веса и оптимизации прочности. По словам японской компании, сетчатый захват руля, ключевой для снижения веса, может быть изготовлен только с помощью 3D-печати LPBF из металла.
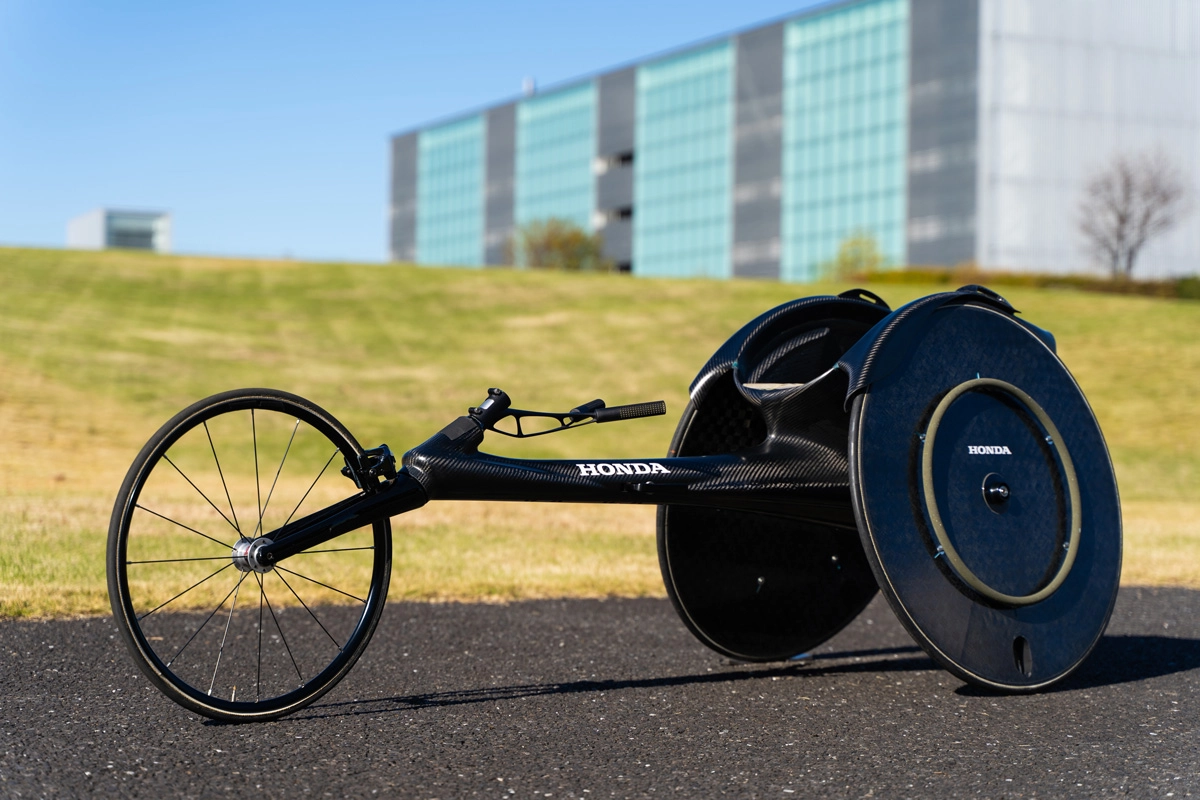
Аддитивное производство для автомобильной промышленности
Роль 3D-печати в автомобильном производстве растет, поскольку автопроизводители стремятся к экономии материалов, средств и времени при создании прототипов, оснастки и конечных деталей.
В декабре 2024 года производитель стержней Laempe Mössner Sinto поставил шесть песчаных 3D-принтеров на литейный завод автомобильного гиганта BMW в Ландсхуте, Германия. Автоматизированная высокопроизводительная линия струйной 3D-печати на связующем может изготавливать песчаные стержни и формы для критически важных компонентов автомобилей. BMW уже использует эту технологию для производства своей последней линейки шестицилиндровых автомобилей. Как сообщается, это решение для аддитивного производства позволяет отказаться от ручных операций, полностью автоматизируя производство и извлечение стержней.
Японский производитель внедорожников Subaru Corporation использовал технологию MultiJetFusionот HP Inc. для 3D-печати деталей для концепт-кара Legacy Outback Boostgear Package. Объявленное на Токийском автосалоне 2024, сотрудничество с HP Japan и DMM.make 3D Print открывает новые возможности аддитивного производства в автомобильном дизайне и производстве.
3D-принтеры HP Jet Fusion 4200 и 5420W позволили компании Subaru отказаться от использования пресс-форм. Как сообщается, это позволяет быстро изготавливать детали с уникальной геометрией. Также был использован нейлоновый материал HP 3D High Reusability PA 12, известный своей жаро- и атмосферостойкостью. Сообщается, что он сочетает в себе необходимую прочность конструкции и 80-процентную степень переработки материала.
Совсем недавно Ford Motor Company, мировой производитель автомобилей, основанный в 1903 году, объявил, что использует 3D-печать для подготовки к своей первой за два десятилетия гонке Формулы-1. Ford уже изготовил более 1000 3D-печатных деталей для автомобилей в своих лабораториях аддитивного производства, , включая пластины охлаждения для аккумуляторов и охлаждающие пластины для других систем. Они будут использоваться в двигателях внутреннего сгорания и гибридных технологиях гоночных автомобилей.