Введение: от мечты к реальности
Аддитивные технологии больше не являются утопической мечтой — они стали реальным инструментом, трансформирующим промышленность. Металлическая 3D-печать, объединяющая инновации в материаловедении, цифровом проектировании и инженерии, уже сегодня переопределяет стандарты в ключевых отраслях, от авиастроения до медицины. В этой статье мы разберем, как это происходит, какие перспективы открываются и почему Россия активно участвует в этой технологической гонке.
Технологии металлической 3D-печати
Современная 3D-печать металлом — это не просто послойный синтез, а сложный процесс, где точность измеряется микронами. Наиболее распространенная технология — селективное лазерное плавление или L-PBF/SLM. Лазерный луч, сканирующий поверхность порошка по заранее созданной компьютерной программе, расплавляет частицы металлического порошка, слой за слоем создавая детали с уникальной геометрией.
Успехи мировых лидеров
Но L-PBF — не единственный метод. Электронно-лучевая плавка E-PBF/EBM использует поток электронов в вакууме, что идеально подходит для работы с тугоплавкими сплавами, такими как титан. А семейство технологий наплавки DED-P/W позволяет восстанавливать изношенные детали, добавляя металлический порошок или проволоку именно туда, где это необходимо.
Эти технологии уже доказали свою эффективность. Например, Airbus с их помощью сократил сроки производства топливных форсунок с шести месяцев до двух недель, а SpaceX использует 3D-печать для создания ключевых компонентов ракетного двигателя Raptor 3.
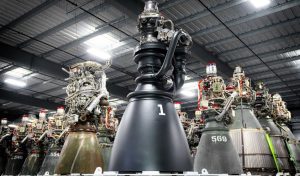
Производство металлических порошков
Часто в основе металлической 3D-печати лежат именно высокотехнологичные порошки. Их производство включает атомизацию (распыление расплава металла в инертной среде), сфероидизацию (придание частицам идеальной формы) и многоступенчатую фильтрацию для достижения однородности. Например, для L-PBF критически важен строгий контроль гранулометрии: размер частиц должен находиться в диапазоне 15–45 микрон, чтобы обеспечить оптимальное спекание и минимизировать пористость.
Титановые сплавы: прочность и легкость
Когда речь заходит о металлической 3D-печати, многие сразу представляют себе титан — и не зря. Сплав Ti6Al4V является, пожалуй, самым известным в этой сфере. Его главный козырь — потрясающее сочетание прочности и легкости. Именно поэтому в авиации, особенно российской, без него никуда — от турбинных лопаток до элементов шасси.
Но что действительно впечатляет, так это медицинские применения. Титановые импланты настолько хорошо приживаются в организме, что со временем костная ткань буквально срастается с ними. Правда, есть нюанс — печатать такие детали приходится в аргоновой среде (или в вакууме, если речь идет о технологии электроннолучевой плавки), иначе металл активно реагирует с кислородом.
Алюминиевые сплавы: легкость и универсальность
Алюминиевые сплавы — совсем другая история. Они легче титана в полтора раза, и это открывает массу возможностей там, где важен каждый грамм. Сплав AlSi10Mg, например, отлично подходит для автомобильных компонентов и авиационных интерьеров. Но если нужна особая прочность, стоит обратить внимание на зарубежный сплав Scalmalloy® — этот сплав со скандием по механическим свойствам приближается к титану, оставаясь при этом значительно легче.
Нержавеющая сталь и жаропрочные сплавы
С нержавеющей сталью ситуация особая. 316L — настоящая рабочая лошадка пищевой и химической промышленности. Из нее делают буквально всё — от форсунок для молочного производства до насосов для агрессивных сред. А вот сталь 17-4PH после печати требует дополнительной термообработки, зато получается невероятно прочной.
Но если говорить о настоящих экстремалах, то это, конечно, жаропрочные стали. Inconel 718 спокойно выдерживает температуры, при которых большинство металлов уже течет как пластилин (более 1000°C). Неудивительно, что его используют в самых горячих точках авиадвигателей и ракетных соплах. Правда, обрабатывать его — то еще удовольствие, обычный инструмент тут быстро сдается.
Российские производители порошков
Что радует, российские производители не отстают. «ВСМПО-Ависма» и «Нормин» делают отличный титановый порошок, «Валком-ПМ» (Русал) освоил производство алюминиевых сплавов, а «Центротех» работает над никелевыми сплавами. Конечно, пока не все получается идеально, но прогресс у всех отечественных производителей очевиден.
Применение 3D-печати в России: космос и атомная отрасль
Если десять лет назад 3D-печать металлами казалась чем-то из области фантастики, то сегодня это уже рабочий инструмент в самых разных отраслях. И что интересно — российские компании не просто пробуют технологию на вкус, а активно внедряют ее в реальное производство.
Возьмем, к примеру, космос. В Роскосмосе уже печатают детали спутников из титана и алюминия — там, где на счету каждый грамм, а прочность должна быть на высоте. Традиционные методы изготовления часто не позволяют создать оптимальную по весу и форме деталь, а вот 3D-печать с этой задачей справляется на ура.
Не отстает и атомная отрасль. В Росатоме напечатанные детали используют в реакторах на быстрых нейтронах. Помните тот самый ТВЭЛ, испытанный в 2022 году? Это был серьезный шаг — доказать, что напечатанные элементы могут работать в таких экстремальных условиях.
Медицинские импланты и инструменты
Но, пожалуй, самые впечатляющие результаты — в медицине. В том же питерском НИИ им. Вредена титановые импланты печатают индивидуально под каждого пациента. Представьте: вместо того чтобы подгонять человека под стандартные изделия, врачи создают имплант, который идеально повторяет анатомию. Реабилитация после таких операций проходит быстрее, а результаты — лучше. Да и хирургические инструменты теперь можно делать буквально «под руку» конкретного врача — из той же нержавейки.
Нефтегазовая и авиационная отрасли
Нефтяники и газовики тоже присматриваются к технологии. Газпром и Роснефть тестируют напечатанные клапаны и элементы насосов — те самые, что работают в агрессивных средах. Оказалось, что коррозионностойкие сплавы, напечатанные на 3D-принтере, порой служат дольше традиционных.
Авиастроители из Ростеха уже используют напечатанные детали в военных самолетах и беспилотниках. Тот же титан — легкий и прочный — идеально подходит для ответственных узлов. В судостроении ситуация похожая: турбинные лопатки, элементы охлаждения — все это уже можно печатать.
Железные дороги и пивоварение
Но, пожалуй, самое неожиданное применение — у РЖД. Они экспериментируют с печатью деталей для локомотивов: от подшипников до элементов тормозных систем. А ведь еще несколько лет назад это казалось чем-то из разряда «когда-нибудь в будущем».
Ремонт с помощью 3D-печати
Отдельная история — ремонт с помощью 3D-печати. Вместо того чтобы менять целую деталь, теперь можно восстановить только изношенную часть. Это и быстрее, и дешевле. В энергетике так чинят теплообменники, в судостроении — гребные валы, а в нефтянке — участки труб. Даже в оборонке технология пригодилась — когда запчасти сложно достать, печать становится настоящим спасением.
Кстати, есть и совсем неожиданные примеры. Та же «Балтика» печатает заготовки для головок розлива пива. Казалось бы, где пиво и где 3D-печать? Но оказывается, и здесь технология находит применение.
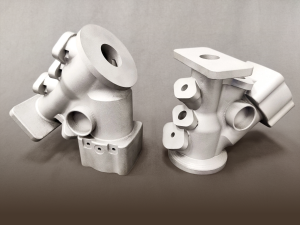
Роль госкорпораций в развитии технологий
Примеры успешных применений можно приводить и дальше, что в очередной раз доказывает, что российские госкорпорации активно внедряют 3D-печать металлами в свои производственные процессы, и это позволяет им решать сложные задачи, снижать затраты и повышать конкурентоспособность. В условиях санкций и необходимости импортозамещения 3D-печать становится стратегически важным инструментом для развития отечественной промышленности.
Оборудование для аддитивного производства
Основой любой аддитивной лаборатории и центра аддитивного производства является 3D-принтер. SLM-установки, такие как те, что представлены на технологической платформе AM.TECH, сочетают в себе высочайшую точность (до 20 микрон) и универсальность, работая с титаном, алюминием, сталью и другими материалами, что делает их пригодными для решения 80% промышленных задач. Эти принтеры полностью соответствуют концепции Industry 4.0, поддерживая автоматизацию процессов и удаленный контроль. Для бизнеса это открывает не только возможность значительной экономии (до 50% за счет сокращения отходов), но и перспективы выхода на новые рынки.
Преимущества 3D-печати: скорость и геометрия
Сегодня металлическая 3D-печать — это не просто технологическая новинка, а реальный инструмент для трансформации производства, способный сократить время выхода новой продукции в десятки раз, а это позволит вам быть намного проворнее конкурентов.
Но дело не только в скорости. Эти технологии открывают возможности для создания деталей со сложной геометрией, которые просто невозможно изготовить традиционными методами. Речь о топологически оптимизированных конструкциях, облегченных элементах с внутренними каналами охлаждения — о тех решениях, которые раньше оставались лишь на бумаге.
Экономия на логистике
Еще один важный момент — логистика. Вместо того чтобы хранить на складах тонны запчастей, можно перейти на модель «печать по требованию». Это значит меньше складских затрат, меньше «замороженных» денег в запасах и при этом — полная готовность к любым запросам клиентов.
Инвестиции в будущее
Оборудование, которое представлено на AM.TECH, — это не траты, а инвестиции с понятной отдачей. Взгляните на опыт SpaceX: они смогли сократить цикл разработки с нескольких лет до месяцев именно благодаря аддитивным технологиям.
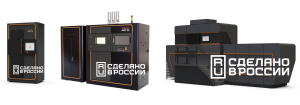
Заключение: промышленная революция XXI века
В заключение хочется подчеркнуть, что металлическая 3D-печать больше не является уделом энтузиастов. Она становится основой промышленной революции XXI века, и Россия, несмотря на все сложности, занимает в этом процессе достойное место. Оборудование, которое уже сегодня выпускается под маркой «Сделано в России», превращает эту революцию из абстрактной мечты в реальный инструмент для развития бизнеса. Если вы еще не задумывались о внедрении аддитивных технологий, сейчас — самое время начать.