Исключительная теплопроводность и электропроводность меди делают её востребованным материалом для аэрокосмической, электронной и энергетической отраслей. Однако её использование в технологиях Laser Powder Bed Fusion (L-PBF) и Electron Beam Powder Bed Fusion (E-PBF) сдерживается высокой отражательной способностью, проблемами с отводом тепла и с пористостью.
С развитием аддитивных технологий, которые всё чаще занимают нишу масштабируемого производства, перед производителями встают вопросы: достаточно ли современных лазерных технологий, усовершенствованных порошков и инноваций в процессах для эффективного использования PBF в стабильной и высококачественной печати медными сплавами? И когда технологии PBF для меди смогут заменить традиционные методы, такие как литьё и механическая обработка? В этой статье мы попытаемся дать ответы на эти вопросы.
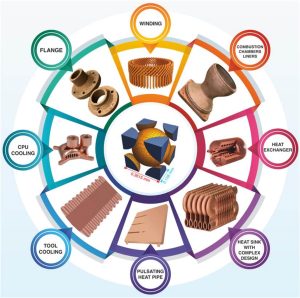
Спрос всё выше
В отличие от традиционного производства, PBF позволяет создавать сложные геометрии и облегчённые конструкции, которые повышают производительность и эффективность, одновременно сокращая отходы материала. Эти технологии также обеспечивают ускоренное прототипирование и сокращение производственных циклов, что уменьшает время вывода на рынок критически важных компонентов.
Растущий спрос со стороны промышленности стимулирует разработку новых составов медных сплавов, адаптированных для АП. Например, сплав Cu-Cr-Zr с добавками Ti, Zr или Nb демонстрируют превосходную прочность и электропроводность. Важным достижением стало использование микролегирования для управления фазовыми превращениями. Исследования Ma и соавторов (2022) показывают, что добавление Y₂O₃ значительно увеличивает плотность дислокаций за счёт несоответствия между матрицей и наночастицами, обеспечивая существенный вклад в общую прочность материала.
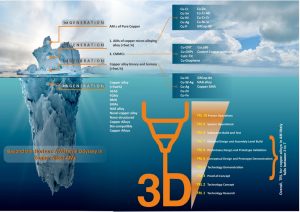
Сплавы Cu-Ni-Sn также находятся в центре внимания благодаря своей коррозионной стойкости и механической прочности. Zhou и соавторы (2023) в своей статье продемонстрировали, что эти материалы можно эффективно использовать в электронике и теплообменниках благодаря уникальным комбинациям свойств. Добавление TiB₂ к Cu–15Ni–8Sn уменьшает размер зерна и улучшает границы высокоугловых зёрен (HAGBs), что способствует синергии прочности и пластичности.
Сплавы Cu-Al с эффектом памяти формы также активно исследуются. Их уникальная способность «запоминать» форму после деформации делает их перспективными для ряда высокотехнологичных отраслей. При этом ключевыми задачами остаются управление текстурой и минимизация пористости. Даже малейшие изменения в составе могут кардинально повлиять на конечные характеристики. Например, добавление Cr или Nb позволяет достичь высокой прочности при сохранении проводимости благодаря выделению наночастиц (Kini и соавторы, 2020).
Отрасли
- В аэрокосмической промышленности, где особенно ценятся высокая прочность и лёгкость материалов, из медных сплавов печатают сопла ракет, системы охлаждения двигателей и теплообменники.
- В электронике и электротехнике при изготовлении печатных антенн, волноводов и радиаторов для схем востребованы их электропроводность и теплопроводность.
- В энергетике и промышленности с их использованием реализуются высокоэффективные решения для охлаждения, печатаются компоненты батарей и электрические контакты.
- В автомобильной промышленности эти материалы находят применение благодаря их коррозионной стойкости и механической прочности.
Особый интерес представляют перспективы создания многофункциональных материалов с уникальными свойствами. Например, использование градиентных композиций Cu–Ni позволяет создавать материалы с контролируемыми характеристиками (Que и соавторы, 2024). Кроме того, развитие новых источников лазерного излучения, таких как синие диодные лазеры, открывает новые горизонты для создания высокоплотных структур (Hori и соавторы, 2021).
Видим цель, но видим и препятствия
Несмотря на очевидные преимущества, масштабирование L-PBF для медных сплавов в промышленности тормозится в силу ряда технических стоп-факторов. Ключевые вызовы и возможные пути их преодоления представлены в следующей таблице:
Проблема | Описание | Решение |
Высокая отражательная способность и проблемы с поглощением. | Медь отражает ~95% инфракрасной лазерной энергии, что затрудняет её эффективное плавление в L-PBF. | Новые зелёные и синие лазерные технологии значительно увеличивают поглощение, что приводит к повышению энергоэффективности и снижению дефектов. |
Теплопроводность и нестабильность расплавленной ванны | Высокая теплопроводность меди (~390 Вт/мК) вызывает быстрое рассеивание тепла, что приводит к неполному сплавлению и слабому сцеплению. | Более высокая мощность лазера и оптимизированные стратегии сканирования обеспечивают более глубокие и стабильные ванны расплава.
Предварительный нагрев платформы минимизирует термические напряжения и растрескивание. |
Пористость, трещины и дефекты окисления | Газовая пористость из-за захваченного кислорода и испаряющихся элементов ослабляет механическую целостность. | Улучшенная защита инертными газами (аргон, азот, вакуумная обработка) снижает окисление и загрязнение. |
Сыпучесть порошка и доступность материала | Медный порошок склонен к окислению и плохой сыпучести, что влияет на качество печати и плотность деталей | Достижения в области газо- и плазменно-атомизированных порошков улучшают согласованность и надёжность в L-PBF |
Теперь рассмотрим эти вызовы подробнее.
Дефекты структуры и их контроль
Одна из ключевых проблем — это дефекты структуры: пористость, трещины и несплавленные частицы порошка. Пористость особенно критична, поскольку она напрямую влияет на механические свойства и долговечность изделий. Точный контроль параметров процесса, таких как мощность лазера и скорость сканирования, позволяет минимизировать этот дефект. Однако даже при соблюдении всех условий полностью устранить пористость удается редко.
Не меньше забот доставляют трещины горячей и холодной усадки, возникающие из-за быстрого охлаждения материала. Несплавленные частицы порошка также остаются актуальной проблемой, снижая качество конечного продукта. В статье Chen и соавторы (2024) выявили несколько типов трещинообразных дефектов в многослойных структурах: внутри зоны плавления, пересекающие границы зон плавления, распространяющиеся до подложки. Эти дефекты зависят от термофизических свойств материалов, таких как коэффициент теплового расширения (CTE), теплопроводность, теплоемкость и температура плавления.
Механические свойства и их оптимизация
Механические свойства медных сплавов, полученных методом АП, варьируются в широких пределах. Прочность может достигать 600 МПа, а относительное удлинение — до 40 %. Электропроводность находится в диапазоне от 30% до 90% IACS (International Annealed Cu Standard, Международный стандарт отожжённой меди), и зависит как от состава сплава, так и от режимов термообработки. Важно отметить, что первый час старения значительно увеличивает предел прочности и предел текучести, но затем эти значения стабилизируются (Yang и соавторы, 2023).
Добавление различных элементов, таких как Cr или Nb, позволяет улучшить комплекс характеристик. Например, сплавы Cu–Cr–Nb демонстрируют высокую прочность при сохранении хорошей проводимости благодаря выделению Cr-наночастиц (Kini и соавторы, 2020). В статье Shen и соавторов (2022) показали, что модификация наночастицами TiC позволяет достичь высокой плотности (более 96%) и улучшенных механических свойств.
Исследования показывают, что микроструктура материала играет ключевую роль в определении его свойств. Например, добавление Y2O3 к Cu-Cr-Zr увеличивает плотность дислокаций из-за большего несоответствия между матрицей и наночастицами, что вносит значительный вклад в общую прочность материала (Ma и соавторы, 2022). Размер зерна и морфология также важны: переход от столбчатых к равноосным зернам позволяет улучшить синергию прочности и пластичности.
Технологические параметры и их роль
Ключевые параметры процесса — мощность лазера, скорость сканирования, размер пятна и толщина слоя порошка — оказывают значительное влияние на результат. Каждое изменение этих параметров может кардинально повлиять на свойства материала. Например, увеличение мощности лазера помогает уменьшить пористость, но одновременно повышает риск образования трещин (Greco и соавторы, 2020). Поэтому поиск оптимального баланса остается одной из главных задач исследователей.
Интересно отметить, что использование синего диодного лазера мощностью 200 Вт для чистой меди позволяет создавать высокоплотные структуры (Hori и соавторы, 2021). Кроме того, стратегия многократного экспонирования снижает шероховатость верхней поверхности с 40 ± 5 до 9 ± 2 мкм (Lintel и соавторы, 2023). Это открывает новые возможности для создания деталей с улучшенными трибологическими характеристиками.
Многолазерные системы и гибридные подходы к производству
Как показывает практика, результат применения технологии L-PBF улучшается за счёт многолазерных систем и лучшего управления лучом. Многолазерные установки L-PBF улучшают распределение энергии, повышая скорость печати и снижая дефекты.
А E-PBF предлагает лучшее управление теплом и снижение трещин, но требует вакуумной среды, что ограничивает его гибкость.
Гибридные методы AП, сочетающие L-PBF с прямым подводом энергии и материала DED, позволяют создавать более крупные и прочные конструкции с лучшим тепловым контролем.
Также всё большую роль в оптимизации процессов играют ИИ и машинное обучение. Мониторинг дефектов в реальном времени с использованием датчиков на основе ИИ позволяет адаптивно управлять параметрами печати. Модели машинного обучения предсказывают и предотвращают пористость, коробление и трещины, повышая успешность печати.
L-PBF против E-PBF: какой процесс более масштабируемый?
Особенность/процесс | Лазерный L-PBF | Электроннолучевой E-PBF |
Источник энергии | Инфракрасный, зеленый или синий лазер | Электронный луч |
Эффективность поглощения | Низкий (для ИК-лазеров) | Высокий |
Вакуум | Нет | Да |
Температурный градиент | Высокий (больше трещин) | Ниже (меньше трещин) |
Масштабируемость | Ограничено рассеиванием тепла | Более перспективно для более крупных деталей |
Последующая обработка
Для улучшения свойств материала часто применяют дополнительную обработку. Горячее изостатическое прессование (HIP) помогает устранить пористость и улучшить плотность материала. Термообработка, включая закалку и старение, позволяет управлять микроструктурой и свойствами материала. Эти методы особенно важны для сплавов Cu-Cr-Zr, где первые часы старения дают наиболее значительные улучшения (Yang и соавторы, 2023).
В статье Li и соавторов (2024) исследовали влияние горячего прессования и ковки на микроструктуру и механические свойства сплавов Cu-3Ag-1Zr. Результаты показали, что термообработка при 420°C снижает плотность дислокаций на 74%, а при более высоких температурах (500–550°C) наблюдается ее дальнейшее уменьшение.
Выводы и прогнозы
Итак, готов ли L-PBF к крупномасштабному производству медными сплавами? В целом – да, в сегменте премиальных высокосложных и ответственных применений, например, в аэрокосмической отрасли, радиоэлектронике, энергетике и медицине. И пока – нет, если речь идет о массовом производстве недорогих деталей. В данном случае затраты на процесс и масштабируемость остаются проблемами для широкого промышленного внедрения.
При этом отметим, что АП медных сплавов продолжает развиваться, предлагая уникальные возможности для создания материалов с новыми свойствами. Однако для полного раскрытия потенциала этой технологии необходимы дальнейшие исследования и разработки. Управление микроструктурой, контроль дефектов и оптимизация технологических параметров с использованием ИИ остаются ключевыми направлениями работы. Будущее этой области зависит от нашего понимания фундаментальных процессов и способности интегрировать новые технологии в производственные процессы.
Адаптированный источник.