«Креативность + итеративная разработка = инновации» – такую формулу вывел основатель международной технологической компании Dyson Джеймс Дайсон. Лаконично и красиво, как это обычно бывает на бумаге. В жизненных же реалиях инновационных компаний в эту формулу укладывается огромный труд всей команды по отлаживанию и оптимизации производственных процессов, повышению эффективности инструментов управления, развитию кадрового потенциала и еще многого всего, без чего невозможно стимулировать креативность и обеспечить результативность каждого шага итеративной разработки. О том, как это работает в ЦАТ, генерирующем инновации в сфере аддитивного производства для ОДК и других корпораций Ростеха, а также за его пределами, рассказал в интервью генеральный директор ЦАТ Алексей Мазалов.
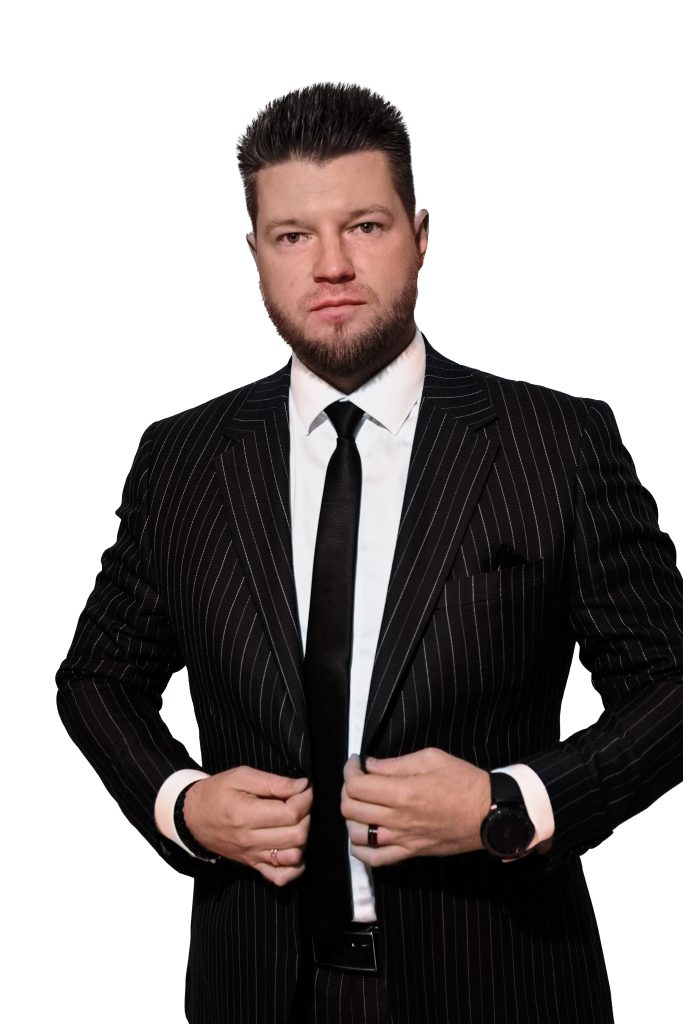
– Вы возглавили ЦАТ в июне прошлого года. Когда вступили в должность, какие сильные стороны компании сразу бросились в глаза, а что, по первому впечатлению, требовало доработки, усиления, изменений? И насколько тогдашние выводы актуальны в настоящий момент?
– При знакомстве с первой линией руководителей внутри компании я увидел сильную, высокопрофессиональную и достаточно слаженную команду, с которой интересно было бы наладить эффективное взаимодействие. Могу с радостью отметить, что нам это удалось довольно быстро, что позволило сосредоточиться на развитии и улучшении процессов, не теряя времени на адаптацию команды. И сегодня мое мнение о компетентности и о силе команды не поменялось. Я стараюсь привносить лишь только те изменения, которые, сохраняя всё лучшее из уже наработанного, способствуют дальнейшему усилению и расширению команды, причем, в первую очередь – с точки зрения производственного, конструкторского, технологического, научного (лабораторного) направлений. В ЦАТ эффективно работает система менеджмента качества, которая поддерживается в том числе инструментами Lean. А сейчас мы взялись внедрять методы канбан. Все эти системы, как известно, подразумевают непрерывный процесс улучшений, что вполне отвечает нашим устремлениям.
– А с чего вы начали?
– К концу минувшего года мы переформатировали деятельность компании, выделив четыре ключевых доходных направления. Первое, безусловно, это аддитивное производство, преимущественно контрактное. Выполняем заказы ОДК и других корпораций, как входящих в Ростех, так и вне его контура. Второе направление – это лаборатория, которая прежде выполняла функции периферии, дополнения к ключевому производству. Теперь, когда мы дооснастили ее парк новым лабораторным оборудованием и усилили штат научных сотрудников, появилась возможность ее большей коммерческой загрузки.
Третий наш столп – конструкторская служба, мы ее за это время значительно усилили. И четвертое – это образовательная деятельность по двум векторам. Первый направлен на повышение квалификации, на усиление компетенций внутри нашей компании. Все новые сотрудники в первую очередь проходят через наш ЦАТовский образовательный центр, что значительно ускоряет их адаптацию на нашей производственной площадке. Второй вектор – коммерческие контракты с другими компаниями на обучение, введение в аддитивное производство их сотрудников. Обучение ведется по ряду направлений: реверс-инжиниринг, проектирование и перепроектирование под обеспечение технологичности аддитивного производства, а также обучаем конкретным технологиям 3D-печати: SLM, DMD, FDM, SLS и печати керамики.
– Усиление конструкторского направления и лаборатории уже дает результаты?
– Когда я пришел в компанию, конструкторское направление, включая реверс-инжиниринг и оптимизацию топологии, было не в фокусе. Теперь же у нас сформирована полноценная конструкторская группа из компетентных, квалифицированных специалистов.
Также мы оснастились дополнительным портативным 3D-сканером, благодаря которому появилась возможность в том числе выполнять выездные задачи на предприятиях. Вот лишь один из примеров. В течение всего лишь полутора месяцев мы разобрали, провели деталировку, сканирование изделия, построили высокоточные трехмерные модели, выпустили комплект чертежей, который преобразовали в рабочую конструкторскую документацию. Что еще важно, выявили химсостав, определили твердость, определили чистоту или шероховатость поверхности. Примерно три недели нам потребовалось на то, чтобы произвести заготовки. Завершающие этапы – финишная обработка, затем – сборка и испытания. На выходе мы импортозаместим два сверхвостребованных на данный момент поршневых двигателя.
– А в саму конструкцию привнесли что-то своё?
– Все литые элементы мы заменили напечатанными металлом из алюминиевых сплавов. Небольшая часть деталей выполнена из пластика. Мы также напечатали и поршень, и цилиндр, причем в формате заготовок под последующую механообработку. Так усилиями специалистов ЦАТ и прежде всего – нашей конструкторской группы удалось упростить, удешевить и ускорить процессы изготовления всех деталесборочных единиц. Экономический эффект можно будет более полно оценить уже при серийном производстве этих двигателей.
– А что стало для ЦАТ открытием года в плане освоения новых технологий, новых возможностей оборудования, материалов и т.д.?
– Здесь я выделю два направления. Первое – это закупка и ввод в эксплуатацию нашей самой большой установки. Это двухъярусная машина, оснащенная четырьмя лазерами по 500 ватт каждый с полем построения 600 мм по трём осям. Это одна из крупнейших машин в SLM; она приехала в начале лета. На ее освоение ушло время, не обошлось без трудностей, но мы их благополучно преодолели. В настоящий момент она поточно изготавливает требуемую для нас продукцию, включая серийную.
– Она загружена полностью?
– Что касается загрузки: весь парк нашего оборудования сейчас загружен более чем на 70%, но по отдельным локальным направлениям — в первую очередь связанным с технологией SLM — уровень загрузки достигает 90%. Показатель в 70% обусловлен тем, что в прошлом году мы только дооснастились несколькими новыми системами и еще просто не успели их загрузить в полном объеме. В текущем году, я уверен, процент загрузки ещё увеличится.
Причём здесь начинает работать следующий важнейший фактор: мы действуем в концепции ТРЦС, то есть территориально распределённых центров специализации. На большинстве предприятий ОДК тоже сформированы свои аддитивные участки; мы работаем в плотной связке с ними и там есть локально недозагруженное оборудование. Поэтому, когда мы внутри ЦАТ перегружены, конечно, мы обращаемся к нашим коллегам в ТРЦС и уже сейчас фактически переразмещаем заказы, чтобы не потерять партнёрские отношения с нашими контрагентами.
Еще одно открытие минувшего года связано с вводом в эксплуатацию габаритной DMD-установки ИЛИСТ-XL. В контуре ТРЦ уже есть подобные машины, и нам было очень интересно получить собственный опыт эксплуатации этой системы. Теперь у нас две габаритные DMD-установки, и уже есть заказы под них. А в текущем году мы загрузим эти две машины и будем дальше делиться заказами с ТРЦС на местах.
– А в целом насколько расширился парк оборудования ЦАТ?
– В прошлом году он пополнился на 14 единиц промышленного оборудования, причем преимущественно это принтеры, позволяющие нам использовать широкий спектр аддитивных технологий, включая технологию печати керамонаполненными фотополимерными композициями.
Ключевое приобретение для нашей лаборатории – рентген-томограф, который позволяет оперативно контролировать внутренний объем исследуемой детали на предмет выявления всевозможных дефектов и несплошностей. Его разрешающая способность составляет до 4 микрон, то есть мы теперь можем выявлять классические аддитивные дефекты, такие как поры и трещины, и заранее отбраковывать детали, если с режимом построения было что-то не так. В томографе можно исследовать изделия габаритом до полутора метров и массой до 200 килограммов. Эта впечатляющая установка изготовлена в России. С ее использованием у нас совершенствуется и ускоряется процесс выходного контроля изделий.
Нас также порадовали отечественные разработчики программного обеспечения. Совместно с командой компании-поставщика мы отладили у себя процессы использования софта для компенсации технологических деформаций в аддитивном производстве. Получилось очень плодотворное взаимодействие, по итогам которого разработчики получили квалифицированную обратную связь от прикладного пользователя и идеи для совершенствования продукта, а ЦАТ – отлично работающее ПО.
– Как строится работа ЦАТ с подразделениями ОДК?
– Я уже упомянул, что мы работаем в концепции ТРЦС. Эти десять территориально распределённых центров специализации на местах – наши точки опоры и «агенты влияния». Проблема в том, что в парках оборудования этих центров разноплановые машины от разных производителей; а когда речь идет о серийном аддитивном производстве, конечно, нужно определиться с ЕТП – единой технологической платформой, на базе которой будут масштабироваться серийные решения. Поэтому для начала было бы правильным документально унифицировать деятельность ТРЦС, чтобы все они работали по одним правилам. Для этого мы уже начали разрабатывать стандарты ОДК по аддитивным технологиям. Первая серия стандартов уже сейчас запущена на согласование по всем ТРЦС. Это стандарты организации по оценке аддитивного оборудования на предмет пригодности к серийному аддитивному производству деталей для авиационного двигателестроения. После того как получим обратную связь от всех ТРЦС, согласуем стандарты в ОДК. И дальше при выборе нового оборудования для ЦАТа и ТРЦС будем ими руководствоваться.
– ЦАТ, работающий под эгидой ОДК, при этом как поставщик продуктов и услуг не ограничен контуром двигателестроительной корпорации или Ростеха. К сожалению, об этом еще мало знают на рынке. Что сегодня делается для расширения круга партнеров?
– Будучи акционерным обществом, ЦАТ, безусловно, стремится к эффективности в финансово-экономическом плане. Понятно, что иной раз для того, чтобы зайти на некий крупный проект, требуются особые стратегии выстраивания партнерства и применяются различные модели ценообразования. Но преимущественно мы придерживаемся нашей сложившейся внутренне утвержденной модели. При этом работаем над ее оптимизацией, чтобы сократить накладные расходы, обеспечить оптимальную себестоимость и, соответственно, выгодную рыночную стоимость продуктов ЦАТа для наших контрагентов.
В основном наша деятельность связана с ОДК, но есть проекты и с внешними партнерами. Например, мы плотно работаем с РосАТ и Роскосмосом по материалам и аддитивному оборудованию, в частности, по SLM-принтерам. До конца 2025 года мы планируем завершить работу по ним, и по итогам будет сделан вывод о пригодности материалов и SLM-систем производства РосАТ для серийного авиационного двигателестроения. В числе наших контрагентов – не только госкорпорации, но и крупные промышленные компании, холдинги и научно-исследовательские институты. Я считаю, что это очень ценно для нас — не зацикливаться только на одной нише и показывать, как в различных отраслях можно реализовывать эффективные кейсы аддитивного производства. К тому же в рамках такого партнерства мы многому учимся друг у друга и перенимаем лучшие практики.
– А с вузами сотрудничаете на тех же принципах?
– Да, реализуем взаимовыгодные инновационные проекты и помогаем друг другу развиваться и наращивать компетенции. Например, в рамках соглашения о сотрудничестве, которое ЦАТ в прошлом году заключил с Институтом машиностроения, материалов и транспорта СПбПУ Петра Великого, запланирована совместная разработка технологии 3D-печати несвариваемых сплавов на высокотемпературном SLM-принтере и восстановления оборотной металлопорошковой композиции методом плазменной сфероидизации. Работы начнутся уже в этом году.
Кроме того, наша компания вступила в Бауманское братство; также состоялось официальное подписание соглашения о сотрудничестве с МГТУ имени Баумана, мы уже принимаем участие в ряде бизнес-мероприятий. Мы также подписали соглашение о сотрудничестве с Самарским аэрокосмическим университетом. Сейчас вместе определяем тематики будущих совместных проектов.
– Студентов технических вузов берете на стажировки?
– Обязательно! И не только студентов. Как правило, стажеры начинают работать непосредственно на машинах в статусе инженера-оператора; потом, после того как стажер осваивает все необходимые ему технологии и оборудование, мы предлагаем ему уже инженерные позиции. За прошлый год, кстати, мы обучили более 350 человек: производственников, конструкторов, технологов, преподавателей и студентов вузов и даже школьников.
– Итак, минувший год, судя по всему, получился для ЦАТа насыщенным, богатым на новации и в целом успешным. Однако путь к успеху обычно пролегает через вызовы разной сложности. Какой вызов оказался самым трудным?
– Пожалуй, тот вызов, который мы бросили сами себе, организовав в октябре первую всероссийскую конференцию «Аддитивные технологии: барьеры и преодоление». Мероприятие прошло в рамках 17-го Международного форума двигателестроения. Вызов был уже в самом названии конференции: мы решили сфокусироваться не на возможностях и преимуществах АП, о которых обычно много и плюс-минус одинаково говорят на мероприятиях подобного рода, а на том, что отечественным аддитивщикам критически важно преодолеть, чтобы аддитивные технологии впредь более активно внедрялись в различных отраслях, в том числе в нашей отрасли авиационного двигателестроения.
Один из таких барьеров, упомянутый многими спикерами, – недопонимание служб главных конструкторов и главных технологов предприятий того, что аддитивные технологии нужно уже сейчас воспринимать как реальный инструмент для производства. Причем не только на этапах научно-исследовательских работ (НИР) или опытно-конструкторских работ (ОКР), но и в серийном производстве.
– Странно! Если скепсис технологов еще можно понять – они больше сталкиваются с ограничениями АП, то конструкторы, для которых с применением этих инструментов открываются такие широчайшие возможности, должны быть обеими руками за!
– Вероятно, это следствие того, что до последнего времени даже в ведущих технических вузах страны будущих конструкторов и технологов практически не обучали аддитивным технологиям. Сейчас ситуация начала меняться; в вузах стали создавать профильные кафедры и читать соответствующие курсы лекций. Но должно пройти время, прежде чем появится заметный результат этих изменений в виде массовой подготовки специалистов, досконально разбирающихся в нюансах применения аддитивных технологий. Ведь у АТ как у любой другой технологии есть возможности, которые нужно четко понимать и эффективно применять. И есть ограничения, которые нужно учитывать при проектировании и изготовлении готовых изделий.
И здесь мы сталкиваемся еще с одним барьером – отсутствием релевантной нормативной базы, учитывающей специфику АП.
– Ну это известная проблема для аддитивщиков, занятых во всех отраслях! Как она проявляется в двигателестроении?
– В авиационном двигателестроении есть три категории безопасности для изготавливаемых компонентов: они бывают прочими, особо ответственными и основными. И для того, чтобы поставить в двигатель деталь, которая дальше будет работать в составе летательного аппарата, необходимо провести общую квалификацию материала и специальную квалификацию. За общую квалификацию ответственен ВИАМ, а за специальную – ЦИАМ.
Что мы имеем в настоящий момент с точки зрения нормативной документации? Даже для ненагруженных деталей, например, кронштейнов или корпусных элементов, относящихся к категории прочих, требования по испытаниям по спецквалификации эквивалентны основным; это значительно удорожает и удлиняет процесс сертификации продукции. Поэтому у нас до сих пор нет возможности говорить о массовом внедрении аддитивных технологий.
В минувшем году по инициативе ЦАТ, поддержанной Минпромторгом России, было проведено совместное совещание под председательством заместителя министра промышленности и торговли с участием представителей ОДК, ВИАМ, ЦИАМ, Росавиации и других заинтересованных сторон. Цель – зафиксировать необходимость внесения изменений в рекомендательные циркуляры норм летной годности, которые регламентируют подходы к определению расчетных значений характеристик конструкционной прочности и в целом к испытаниям 3D-печатных деталей. И еще важный момент – наделить Росавиацию полномочиями утверждения этих документов. Рассчитываем на ощутимые подвижки в этом направлении уже в этом году.
То есть один из главных вызовов – это переформатирование нормативной документации, и мы со своей стороны сделали необходимые шаги.
– Кстати, обратимся к мировому опыту. Пока у нас в муках рождается релевантная нормативная база для АП, Китай идет по пути не просто укрупнения, а гигантизма. Для них аддитивная фабрика, где стоят сотни принтеров и практически в условиях безлюдного производства серийно печатают готовые изделия – уже привычный формат. Но насколько эта реальность была бы релевантна для наших условий?
– При устранении барьеров, о которых мы сейчас говорили, у нас это вполне достижимо. Преодолев эти барьеры, мы сможем перейти к формированию единой технологической платформы. И в итоге наступит момент, когда мы сможем масштабировать серийное производство деталей авиационных двигателей.
Беседовала: Светлана Бакарджиева.